CWI Generation4™ Welding Wires are designed for use in many different welding processes. The three most common types of welding used with our stainless steel and nickel welding alloys are Tungsten Inert Gas (TIG), Metal Inert Gas (MIG) and Submerged-Arc Welding (SAW). To ensure that you select the proper welding consumable alloy to work with your welding process, a brief description of each process is listed below. If you need further information on the specific welding parameters (Diameter, Voltage, Amperage, and Gas) recommended for each CWI Generation4 ™ Alloy, visit our recommended welding procedures page.
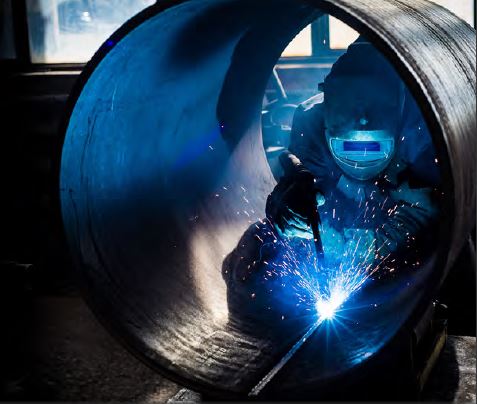
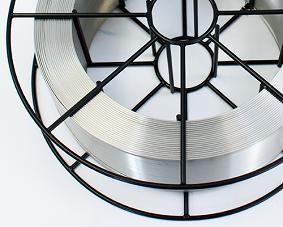
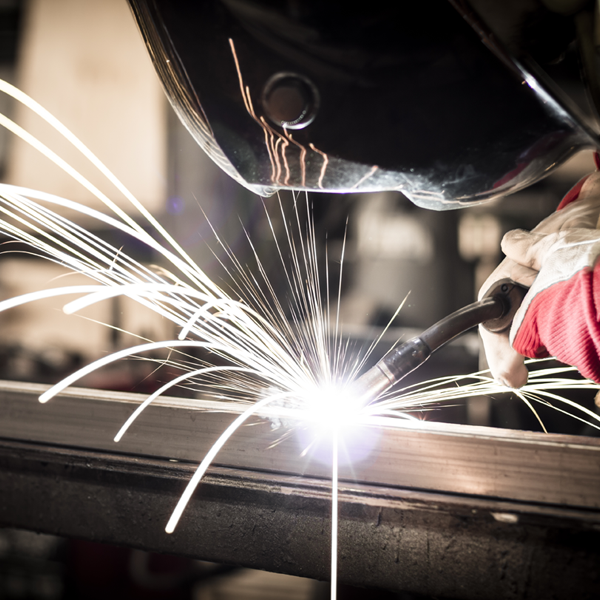

TUNGSTEN INERT GAS (TIG) WELDING
Also known as Gas Tungsten Arc Welding (GTAW), TIG welding uses a tungsten electrode, a filler metal and an inert shielding gas (such as argon or helium) during the welding process. This method requires a highly skilled welder, as the manual technique requires two hands to utilize the equipment and apply the filler metal to create the weld joint. TIG welding is typically used with stainless steels and non-ferrous metals, on thinner section of metal, and provides the welder greater control over the properties of the weld versus other similar processes. It has the disadvantage of being relatively slow due to it’s complexity and multi part process.
METAL INERT GAS (MIG) WELDING
Also known as Gas Metal Arc Welding (GMAW), the MIG welding process employs a welding gun, a power supply, an electrode (alloy wire) and a shielding gas. The welding procedure is uncomplicated, with the welding gun bringing all the required components (power, filler metal, shielding gas) together at the weld point. Compared to other methods, training for MIG welding requires less time to develop a usable skill level in the field. It is the preferred welding method in most industrial applications, and can be easily adapted to automation if required. Issues with dross and porosity of welds can affect the quality of the finished welds, so additional scrutiny of materials and cleanliness is required.
SUBMERGED ARC (SAW) WELDING
Often called Sub-Arc Welding, the SAW welding process is primarily an automated method of welding that isolates the arc zone below (sub) the surface of a molten flux, eliminating atmospheric contamination. The process uses a continuous feed of consumable welding wire in either a single or multiple wire/alloy combination. SAW has the advantage of a high deposition rate and deep weld penetration, making for a high ft/min welding rate. It also allows for single pass welds with thicker material. SAW is limited by the plane of the welding operation (straight welds are preferred) and can result in the need for an added slag removal step.
Wire Diameters by Welding Type
MIG (GMAW) Diameters | TIG (GTAW) Diameters | SUB ARC (SAW) Diameters | |||
---|---|---|---|---|---|
Imperial in. | Metric mm | Imperial in. | Metric mm | Imperial in. | Metric mm |
0.023 | 0.6 | 1/16 | 1.6 | 5/64 | 2 |
0.030 | 0.8 | 3/32 | 2.4 | 3/32 | 2.4 |
0.035 | 0.9 | 1/8 | 3.2 | 1/8 | 3.2 |
0.045 | 1.14 | 5/32 | 4.0 | 5/32 | 4.0 |
0.047 | 1.2 | 3/16 | 4.8 | ||
1/16 | 1.6 |