One of the most rewarding feelings in the world is restoring an old collector’s car and creating that cross between new and antique look that car buffs are looking for in their garages or driveways.
Restoring classic cars has been popular forever, with many TV shows, Facebook groups, and YouTube channels focused on salvaging older cars, doing some auto body repair, and getting them back on the road.
Beyond sourcing parts and deciding on paint, interior design and other aesthetic features, one of the main tasks is welding repairs. There are plenty of body shops capable of doing this, but many car restoration jobs are preferably done by the individual.
Continue reading to learn about some of the best tips for frame welding, and how best to weld a classic car to ensure the on-road performance lasts as long as desired.
The Challenges of Welding Old Cars
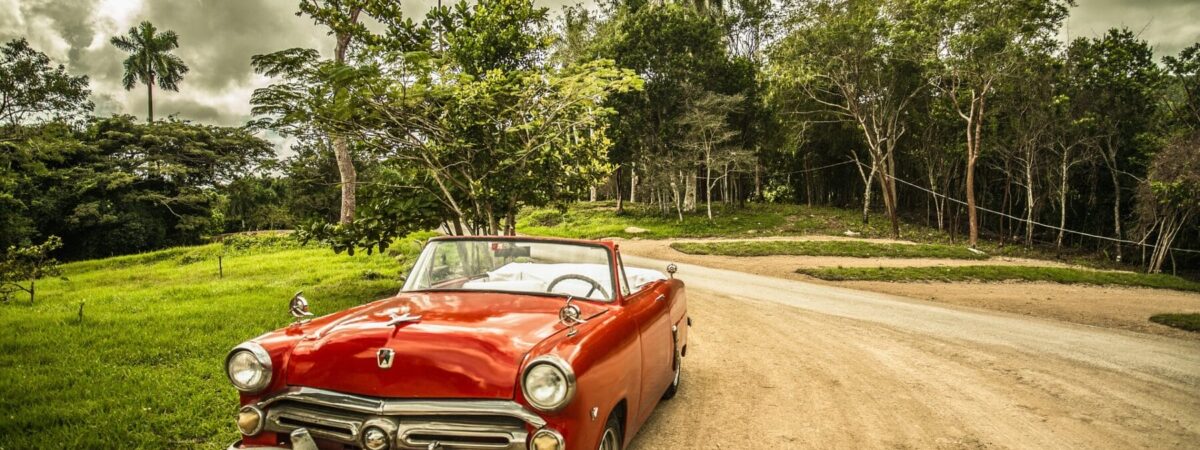
The enjoyment and satisfaction of working on an old car is met with a few obstacles before the finished product is done. Let’s take a look at a few of the things standing in your way if you choose to restore an antique or classic car.
Disassembly
Many times, with either older or damaged cars, simple and quick repairs are simply not possible. Whether it is because of rust, deterioration, or the need to replace parts deeper within the car, these projects are often not that straightforward.
To properly fix a vehicle that hasn’t been taken care of or is simply too old to be in good condition, a full disassembly is often the easiest, or only way to do it. Although this allows for a cleaner slate, and a better understanding of issues, this requires a lot of auto body repair work at the end to get it moving again.
For these longer and more tedious welds, where the integrity of your entire project relies on durable and high-quality Welding Wire, like CWI’s.
Removing and Preventing Rusting
With many vehicles, especially older ones, rusting is a major aesthetic and structural issue and concern. Even with corrosion resistant materials like stainless steel or nickel, rust can occur.
Beyond just making a car look less clean and new, rust can slowly cause deterioration and structural damage, leading to more repairs than anticipated.
There are a few ways to prevent rusting when doing any car body welding. The best way is to fully clean and prep your surface before beginning a welding process. Many metals have thin layers that give them corrosion resistance qualities, but these can be removed by mistake during welding.
An example is stainless steel which has a layer of chromium oxide protecting it. This acts as a protective seal against rust in the welding process and beyond but can be removed during the heating or cooling process of welding. Thorough cleaning and prepping of your surface ensures that this does not happen.
Carbide Precipitation
Carbide precipitation can cause serious issues during any welding process. Typically occurring at extreme heats, it happens when chrome and carbon are drawn out of the welding material and react to the atmosphere.
This phenomenon can not only reduce corrosion resistance on the metals being welded, but can reduce mechanical properties as well, leading to reduced ductility and toughness of even premium metals.
Using an alloy like our GEN 316LSI alloy can help prevent carbide precipitation, as its low carbon content offers corrosion resistance against it.
Wetting Action
A priority to avoid disappointing welding results is to create an improved wetting action. Wetting is crucial to the bonding or adherence of any two materials. It is described as the ability of a liquid to maintain contact with a solid surface, resulting from intermolecular interactions.
Good wetting out of your Welding Wire material will allow it to flow nicely into the parent metal. This promotes a seamless transition, as the outside edges of the weld will form together.
A higher silicon alloy is best for wetting, and our GEN308LSI alloy produces a very smooth weld profile when used in MIG Welding.
MIG Welding for Cars

Whether you’re a beginner or a professional, MIG Welding (Metal Inert Gas Welding) is the best-suited technique for car frame welding.
MIG Welding produces strong and reliable welds, while being suitable for many materials such as steel, aluminum and stainless steel. This material versatility allows for use on cars from different eras which may have different physical make-ups.
This technique can be used in both repair and fabrication work as well, making it a good option for restoration projects that may require a full body reconstruction due to previous car damage.
MIG Welding, although thought to be a beginner’s weld, does require the correct wire feed speed, voltage, and shielding gas flow rate to be successful.
For any questions or concerns about different welding techniques or these specific adjustments, our guide to recommended welding procedures is here!
The Popularity of Car Restoration
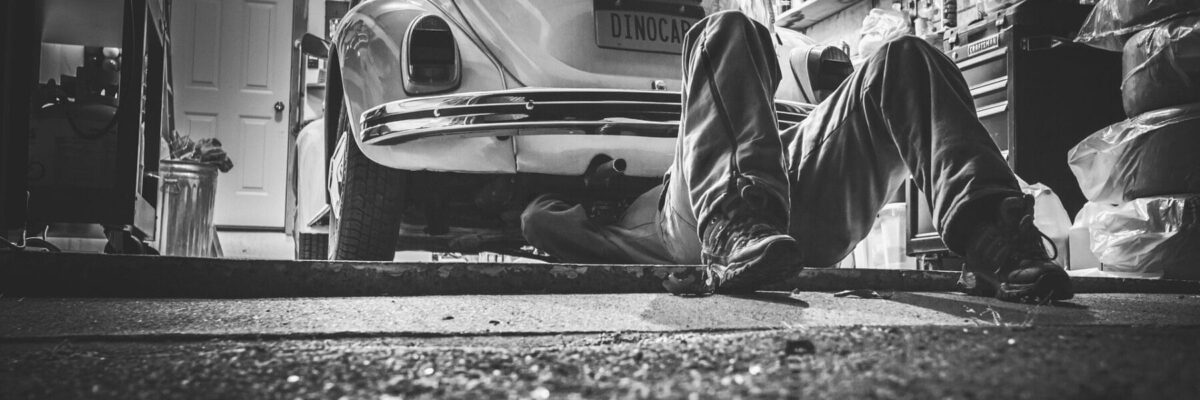
Especially as repair technologies have improved over the years, restoring old cars has only grown in popularity. There are countless garages across the world taking old cars in to try and bring them back to life.
There are websites and social media groups dedicated solely to cars from as old as the start of the 1900s that have been completely restored and look almost brand new.
Car shows and auctions are littered with vehicles that many may have scrapped, but with some long hours of repairs are becoming antique pieces and collector’s cars.
Whenever you’re out driving, it is rare to hear “oh, look at that 2018 Civic”, but seeing a retro vehicle that has been spruced up is far more likely to catch the eye.
With how many hours and how much dedication goes into these personal restoration missions, it is undeniable that reliable materials are important. That is why CWI Welding Wire products are the right choice for a project that means this much.
For an in-depth look at the popularity and process of restoring an old car, check out this article from Pedal Commander.
Why CWI GEN4™ Welding Wire is the Answer
Boasting strength and adaptability among other notable qualities, Central Wire’s Generation4™ Welding Wire has an alloy to meet the requirements of any application.
The quality of our Welding Wire products is unmatched. It is manufactured to exact specifications and supplied with a certificate of conformance stating physical and mechanical properties. As with all our other products, our welding line is manufactured to ISO9001:2015 industry standards.
We offer a variety of packaging options for your convenience, including reels, spools and drums. Find a full list, as well as multiple instruction sheets and brochures on our product page here!
If you’re ready to take on that car restoration project you’ve been planning forever, then you need reliable Welding Wire products that will work as hard as you. Request a quote with us today or contact our sales team with any additional questions you may have: sales@centralwire.com.