At Central Wire Group of Companies, we specialize in manufacturing premium alloys tailored to meet the demanding needs of industries where performance and reliability are non-negotiable. With our focus on delivering high-quality, custom solutions, we leverage advanced machining capabilities and expertise to produce alloys that excel in even the toughest environments.
Whether you need a durable product for mission critical Aerospace applications, or reliable performance in the various Commercial industries we serve, you can trust that Central Wire has an alloy built for your project conditions.
One of the stars of our alloy lineup is Inconel® 718. This versatile Nickel-based alloy can handle harsh industry conditions and temperatures, without compromising performance.
Continue reading to discover the capabilities unlocked by choosing Inconel® 718.
Inconel® 718 Qualities
Alloy 718 is an austenitic Nickel-based superalloy, designed primarily for its strength in extreme temperatures. A precipitation hardening alloy, 718 displays exceptionally high yield, tensile and creep-rupture properties at temperatures well below freezing, and up to and beyond 1300°F (704°C).
As a specialty alloy, Inconel® 718 has improved mechanical short and long-term properties vs. other Nickel alloys and possesses great fatigue strength in the age hardened conditions. The material combination includes very specific mixtures of niobium, molybdenum, titanium and aluminum to assist with performance properties, as well as precipitation hardening.
A very versatile solution, Alloy 718 is available in many forms, and produces consistent performance in a range of extreme applications.
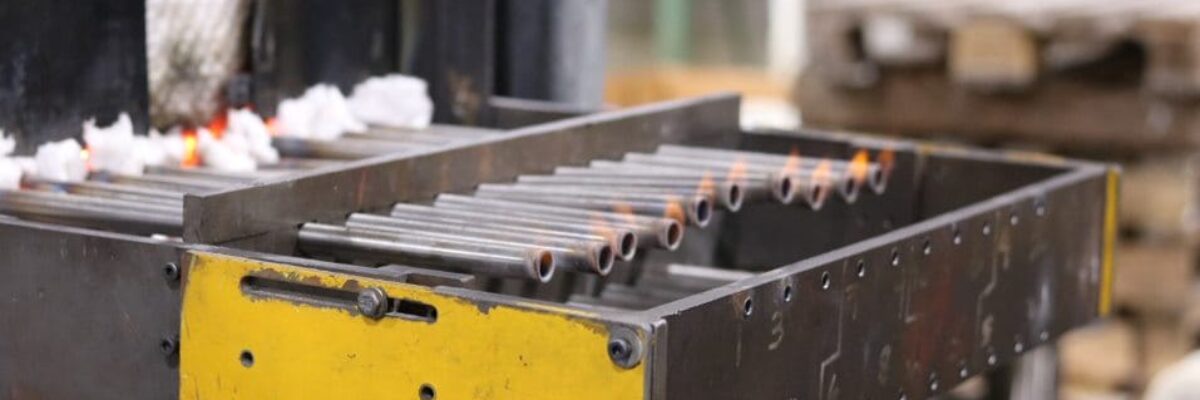
Chemical Composition
Cb: 4.75-5.50%, Cr: 17.0-21.0%, Mo: 2.8-3.3%, Ni: 50.0-55.0%, Ti: 0.65-1.15%
Qualifying Specifications & Standards
Depending on the standards applied and the form of material, Alloy 718 can be specified through many of the following:
Standard | Designation |
EN | 2.4668 – NiCr19FeNb5Mo3 |
ISO | NiCr19Nb5Mo3 |
UNS | N07718 |
AMS | 5662, 5663 |
ASTM | B637 |
AWS/SFA | 5.14 |
Applications
Many of the common uses of Inconel® 718 are applications where temperature would stress the performance of traditional Nickel or Stainless alloys. 718 is able to maintain both its high strength and corrosion resistance even as the operating temperature increases. Strength qualities are maintained up to approximately 1300°F (704°C), and effective corrosion resistance remains intact up to approximately 1800°F (980°C).
These unique high temperature qualities make Inconel® 718 a high-demand material for components used in Aerospace, Oil and Gas and Industrial applications. Some of the most common applications of the alloy include:
- Engine and machinery components
- Gas turbine blades and other parts
- Aerospace fasteners
- High-temp filtration mesh
- Refinery equipment
- Cryogenic tanks, pumps, and valves
- Liquid rocket components
- Compressors and other high-pressure equipment
Alloy 718 can also be used for welding consumables, due to its superior resistance to post weld cracking.
Availability & Forms
Alloy 718 is a stocked product. Lead times vary based on processing required to finished form, but raw material is available at many of our ISO9001 certified manufacturing locations. Central Wire is able to make Alloy 718 available in the following forms:
- Drawn Wire
- Drawn Fine Wire (.001″ – .020″)
- Rolled Strip
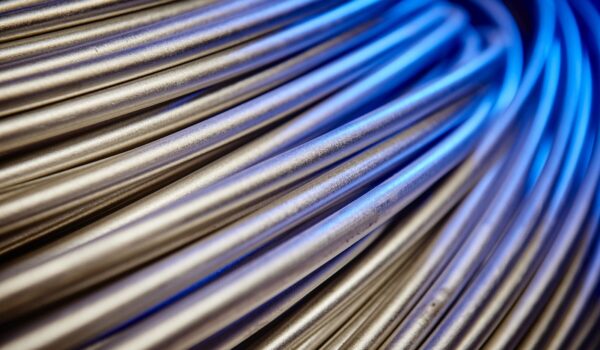
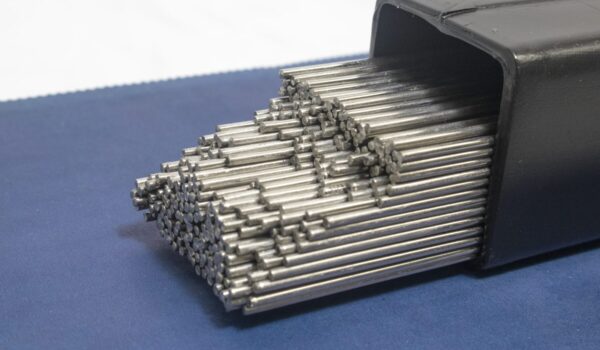
Investing in a Premium Heat-Resistant Alloy
Choosing Inconel® 718 promises durable performance over a large temperature range. Added strength, corrosion resistance, high yield and creep-rupture properties allow for the various applications of this alloy. Contact our sales team at sales@centralwire.com with any questions you may have about the performance and durability of this alloy, or others in our lineup.
To kickstart your next project with a product that is built to last, Request a Quote with us today!