CWI Generation4™ Welding Wires are designed for use in many different welding processes. The three most common types of welding used with our stainless steel and nickel welding alloys are Tungsten Inert Gas (TIG), Metal Inert Gas (MIG) and Submerged-Arc Welding (SAW). To ensure that you select the proper welding consumable alloy to work with your welding process, a brief description of each process is listed below. If you need further information on the specific welding parameters (Diameter, Voltage, Amperage, and Gas) recommended for each CWI Generation4 ™ Alloy, visit our recommended welding procedures page.
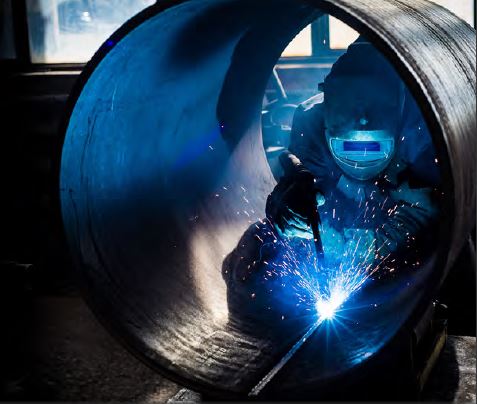
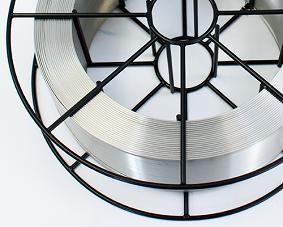
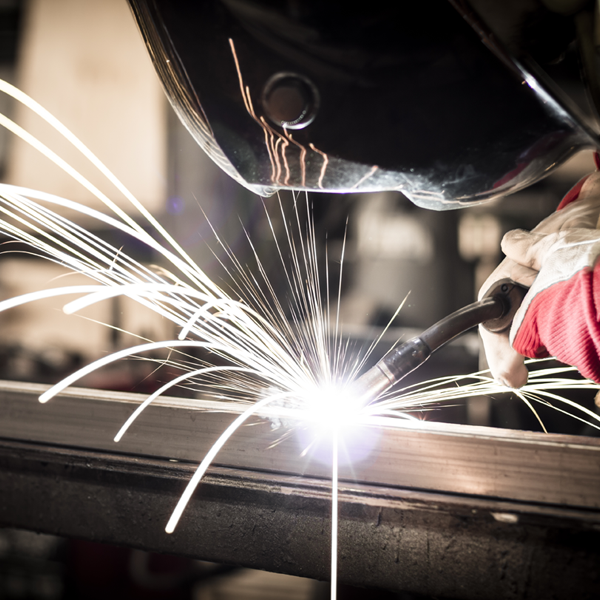

TUNGSTEN INERT GAS (TIG) WELDING
也被称为 钨极气体保护焊 (GTAW), TIG welding uses a tungsten electrode, a filler metal and an inert shielding gas (such as argon or helium) during the welding process. This method requires a highly skilled welder, as the manual technique requires two hands to utilize the equipment and apply the filler metal to create the weld joint. TIG welding is typically used with stainless steels and non-ferrous metals, on thinner section of metal, and provides the welder greater control over the properties of the weld versus other similar processes. It has the disadvantage of being relatively slow due to it’s complexity and multi part process.
METAL INERT GAS (MIG) WELDING
也被称为 气体保护金属电弧焊 (GMAW), the MIG welding process employs a welding gun, a power supply, an electrode (alloy wire) and a shielding gas. The welding procedure is uncomplicated, with the welding gun bringing all the required components (power, filler metal, shielding gas) together at the weld point. Compared to other methods, training for MIG welding requires less time to develop a usable skill level in the field. It is the preferred welding method in most industrial applications, and can be easily adapted to automation if required. Issues with dross and porosity of welds can affect the quality of the finished welds, so additional scrutiny of materials and cleanliness is required.
SUBMERGED ARC (SAW) WELDING
通常被称为 亚弧焊,SAW 焊接工艺主要是一种自动化焊接方法,可隔离熔融焊剂表面下方(子)的电弧区域,从而消除大气污染。该工艺使用单根或多根焊丝/合金组合的自耗焊丝连续进给。 SAW 具有熔敷率高和焊缝熔深深的优点,可实现高 ft/min 焊接速率。它还允许使用较厚的材料进行单道焊接。 SAW 受焊接操作平面的限制(首选直焊),并可能导致需要额外的除渣步骤。
不同焊接类型的线径
MIG (GMAW) 直径 | TIG (GTAW) 直径 | SUB ARC (SAW) 直径 | |||
---|---|---|---|---|---|
帝国在。 | 公制毫米 | 帝国在。 | 公制毫米 | 帝国在。 | 公制毫米 |
0.023 | 0.6 | 1/16 | 1.6 | 5/64 | 2 |
0.030 | 0.8 | 3/32 | 2.4 | 3/32 | 2.4 |
0.035 | 0.9 | 1/8 | 3.2 | 1/8 | 3.2 |
0.045 | 1.14 | 5/32 | 4.0 | 5/32 | 4.0 |
0.047 | 1.2 | 3/16 | 4.8 | ||
1/16 | 1.6 |