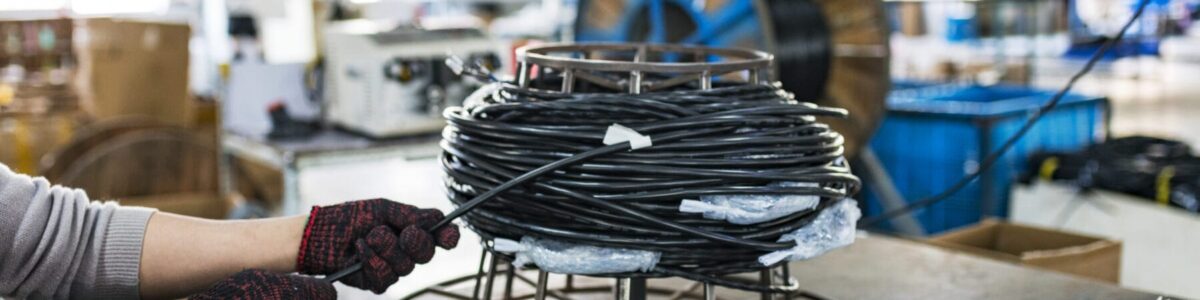
A common question we receive is, ‘We know you do both nylon and vinyl coatings on cable, but why would I choose one over the other?’ Coated cable refers to when a plastic jacket is applied to the exterior of cables to increase chemical resistance, flexibility and strength.
In our case, we produce custom jacketed aircraft cable and wire rope in nylon and vinyl thermoplastic jackets.
Both vinyl and nylon have advantages, making it difficult to choose between the materials. If you are getting ready to place a coated cable order at https://sanlo.com/contact/, and you’re not sure which style to choose, continue reading for the key differences you should know.
Nylon
Nylon is an extremely durable material that is resilient to abrasion and impact. It offers a long cycle life, especially in high-use environments where it moves along pulleys or sheaves. It can withstand harsh conditions as well as temperature shifts while remaining intact and in use.
A nylon coated cable includes a core wire wrapped in a protective nylon casing. The casing creates a cable with high tensile strength capable of withstanding heavy loads and tension. The coating features a textured surface and is robust and durable. Even though nylon cables have a strong coating, they remain flexible enough to use in many different ways.
People commonly use nylon in exercise equipment and conveyor systems. It can also withstand acidic environments and has strong chemical resistance, making it suitable for toxic and acidic applications. Nylon coated cable is best used indoors because it can crack easily when exposed to light.
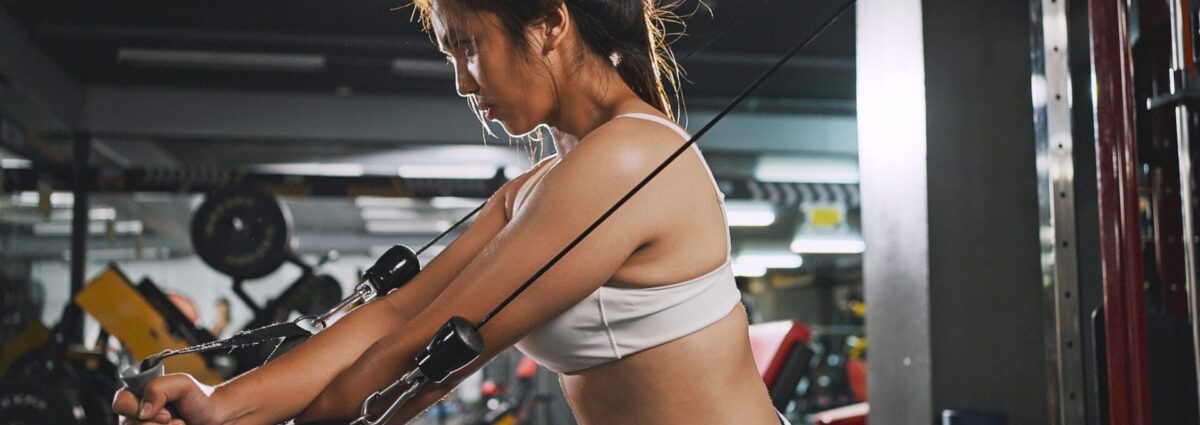
Advantages to Nylon Coating:
- 力量
- Abrasion Resistance
- Chemical Resistance
- Longevity
Applications and Industries using Nylon Coating:
- Pulleys (ex. gym equipment, conveyer pulleys)
- Acidic Environments (ex. sewers, wells)
- Indoors (low UV resistance)
Polyvinyl Chloride (Vinyl)
Vinyl is softer and traditionally more flexible than Nylon. Vinyl is an excellent general-use material, and usually less expensive than Nylon, too. Though vinyl coating may experience shredding, it still withstands tension and abrasion to a certain degree in its applications.
A vinyl coated cable is a core wire wrapped in a vinyl casing. The casing is smoother, and more uniform compared to a nylon coating, resulting in a softer exterior layer. To avoid abrasion and other damage, these coatings can come in slightly thicker varieties. Vinyl coatings also have a glossy finish, making the appearance much different than the nylon alternative.
People use vinyl coating cable outdoors more than indoors because of its high UV resistance. Although it may not be as strong or durable, this cable makes up for it with flexibility and resistance to moisture. These features suit it for use in wet conditions or when it needs to be shaped differently than a nylon coating.

Advantages to Vinyl Coating:
- Flexibility
- Electrical Insulation Properties
- Moisture Resistance
- Low Friction (smooth surface)
Applications and Industries using Vinyl Coating:
- Telecommunications
- Industrial Machinery
- Sailing and Towing
- Outdoors (high UV resistance)
Specifics of CWI Coated Cable Products
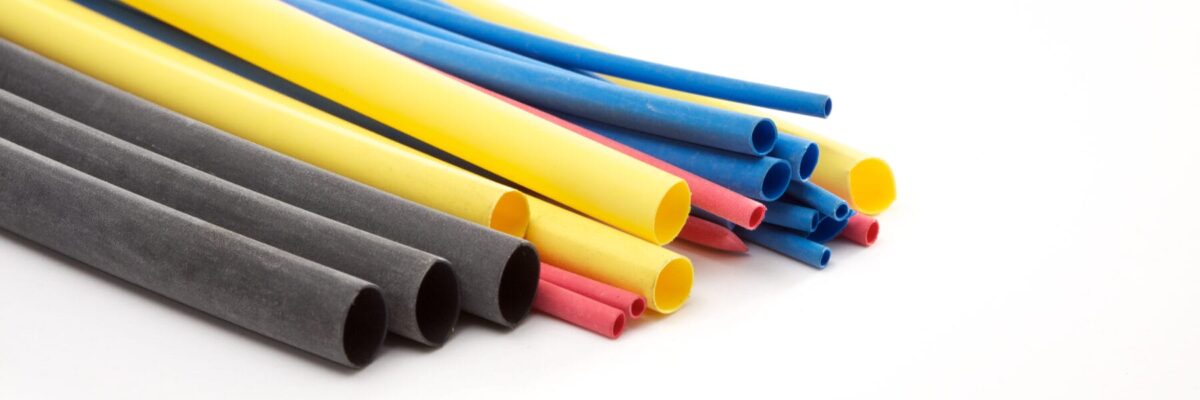
Nylon and vinyl are both available in a variety of standard colors in addition to custom color-matched hues. Our coating capabilities range from 0.018” up to 3/4” outer diameter, and jackets can be applied to galvanized or stainless-steel cables of varying constructions and diameters.
It is important to note that coating a cable increases its tolerance to friction and wear, but it does not intrinsically increase its breaking strength.
The nominal strength of a jacketed aircraft cable is still based on its diameter, construction, and material prior to coating, meaning a 3/16” cable coated to 1/4” does not develop the inherent strength qualities of a 1/4″ cable.
For more information about the color selection, tolerances, and configurations of our coated cable, visit our product page! Contact us with any questions, or start a quote today!