Welding presents very unique challenges, many of which revolve around using the right material so that your weld lasts and maintains over a long period of time. One material that can present some challenges is welding using stainless steel.
Stainless steel is a popular building material that has long been praised for its strength and corrosion resistance. However, welding with this attractive metal comes with its own set of obstacles that must be considered before embarking on a project. Whether it is MIG welding, TIG welding, or another welding technique, there are issues that can arise in steel welding.
Let’s take a closer look at some of the ways to overcome the challenges of stainless steel welding with our custom alloys.
Choosing a Welding Process
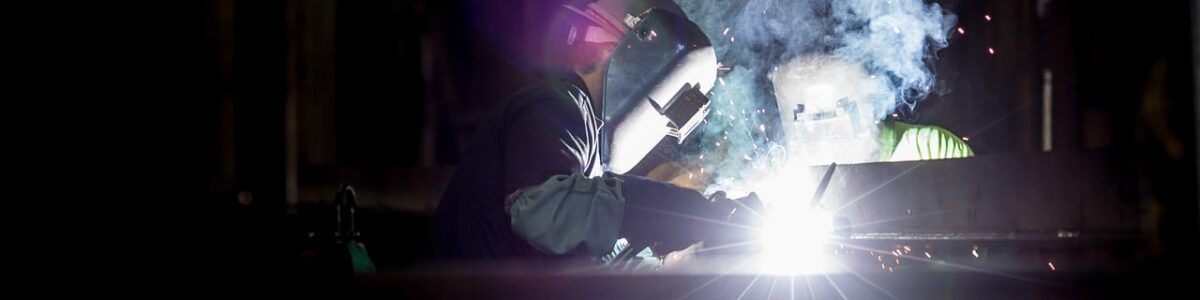
Before you begin, you will want to determine which process you’re going to be using. Stainless Steel can be welded with submerged arc welding (SAW), tungsten inert gas welding (TIG), and gas metal arc welding (MIG). Each of these processes will yield a slightly different result.
To decide which is the best process, consider: the welder’s skill level, the aesthetics of the final piece including bead appearance, the thickness of the metal plus the costs and timing factors of the project. If artistry is paramount, then the finesse of TIG welding could be a good fit, but if speed and efficiency are a priority, then MIG welding may be a better process.
To learn more about whether you should choose TIG Welding vs MIG Welding, you can read our article comparing the two welding methods.
Cleaning to Avoid Rusting
Under normal conditions, stainless steel is known to withstand corrosions of all kinds. However, in extreme circumstances, stainless steel can rust.
This occurs when the chromium oxide layer – the element that protects stainless from rusting – is destroyed or removed. Sometimes this can happen during welding, either during the heating or cooling process. To combat this, you may want something with a high chromium content like our GEN 310 alloy.
Even with TIG welding, rust can be one of the biggest challenges of welding with stainless steel. That’s why cleaning and prepping your stainless before you start is so important. With a properly cleaned and prepped piece of stainless steel, the chromium oxide inside acts as a protective seal against rust during the welding process. It can help the stainless heal itself from discoloration and permanent marks.
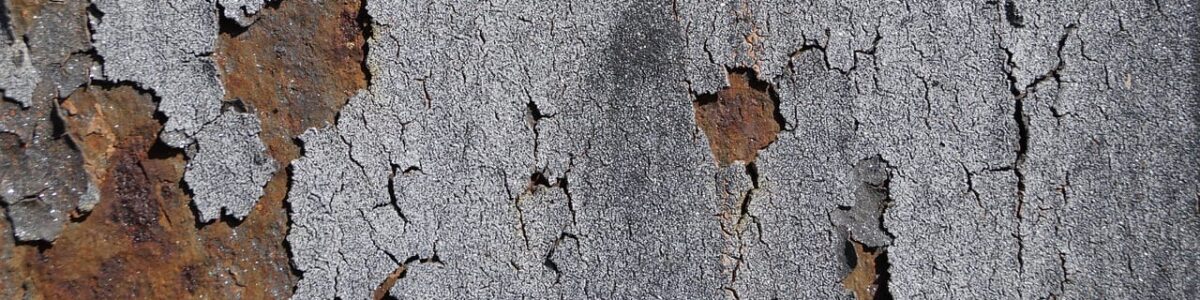
Occurring typically at extreme heats, carbide precipitation is a major concern with stainless steel welding. It occurs when the chrome and carbon in the stainless steel are drawn out of the material and react to the atmosphere.
With austenitic stainless steels, intergranular attack is usually the result of chromium carbide precipitation (Cr23C6) at grain boundaries, which produces a narrow zone of chromium depletion at the grain boundary.
With our GEN 316LSI alloy, the low carbon content offers excellent corrosion resistance against carbide precipitation. Higher productivity could certainly be realized in the MIG welding process. With improved wetting action, it could be even better.
Wetting is crucial to the bonding or adherence of any two materials. It is described as the ability of a liquid to maintain contact with a solid surface, resulting from intermolecular interactions.
Good wetting out of the welding wire material will make it flow nicely into the parent metal. This is important as the outside edges of the weld will form or flow and make almost a seamless transition. For this, you’ll want an alloy with a higher silicon content for improved wetting action. Our GEN 308LSI is great for general purpose MIG welding because it provides a nice and smooth weld profile.
Large Overlay Applications
If you’re depositing one or more layers of metal with specific characteristics on a base metal, this stainless steel (GEN 317L) is often used for large overlay applications and welding base metals with similar chemical composition.
It has a lower carbon composition which reduces the possibility of intergranular carbide precipitation, which in turn increases the resistance to intergranular corrosion. And it even resists pitting and crevice corrosion.
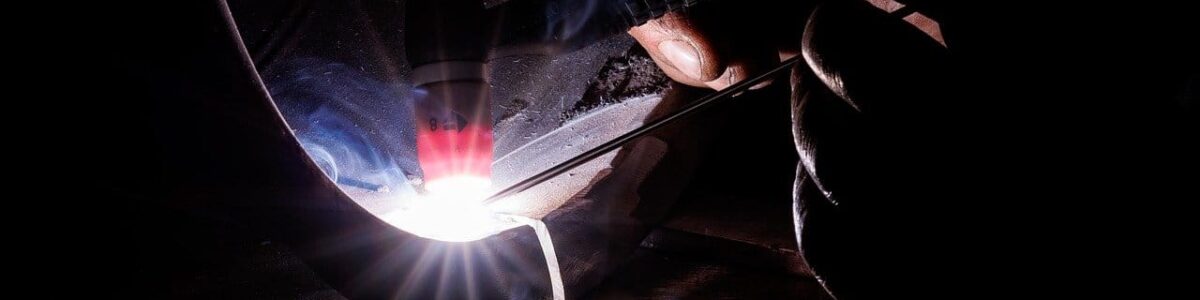
One way to prevent warping when welding stainless-steel is to clamp a piece of brass or copper behind the seam of the weld. This will serve as a cooling mechanism or “heat sink", absorbing the heat while preventing any burn through. It could also help you weld the entire seam continuously.
Get a Quote Today!
At CWI, we carry a variety of metal wire including: Acier inoxydable, Copper, and Nickel. We also have a wide variety of specialty alloys, manufactured specifically for harsh conditions and demanding applications.
As you can see, there are a lot of obstacles that come with Stainless Steel welding. However, Central Wire has you covered with a variety of different products to suit your welding needs.
Take a moment to review our new Stainless Steel welding page, explaining alloys such as GEN 308LSi, GEN 316LSI, and GEN 317L.
Feel free to contact us for any additional welding questions you may have at sales@centralwire.com. If you’re ready to invest in your welding wire solutions, request a quote with us today ici! Let us help you overcome the challenges of stainless steel welding.