As a company that manufactures wire for numerous industries, having a range of alloys that are specifically catered to prevent corrosion is crucial to ensure our customers can find exactly what they need. First, it’s important to understand why metals can corrode.
Metals can corrode for numerous reasons, especially in harsh conditions. Examples of typical metal corrosions include metal reacting with a substance like oxygen, or a metal being placed under too much stress causing the material to crack.
At CWI we have the corrosion resistant metal alloys you need to ensure long-lasting performance even in the harshest of conditions. Our research and years of manufacturing experience promise materials that can withstand corrosive environments.
Today’s Challenges
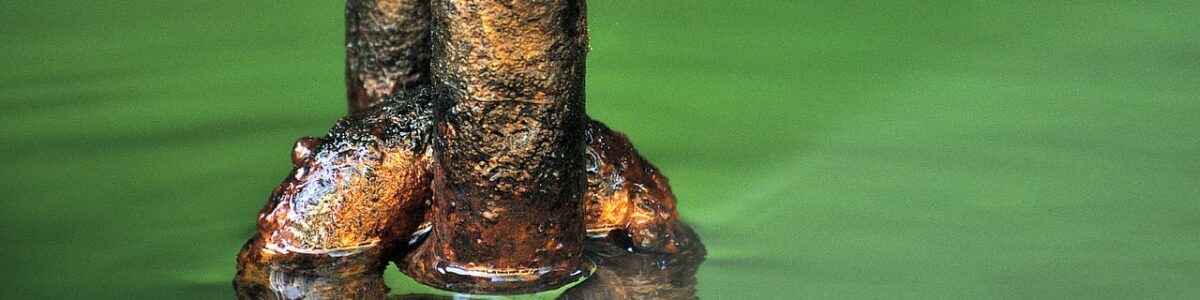
As industries around the world push for higher and higher levels of performance in their materials, metallurgists continue to develop new and exciting alloys to meet today’s challenges. Regardless of the environment, strain, or temperature that today’s specialty metals need to operate in, there are choices available to engineer a range of solutions in a variety of applications.
Combining the global resources of the Central Wire Group of Companies, with our Metallurgical knowledge and manufacturing experience, we can provide the highest quality solutions, including the right alloy for your application every time.
Main Industries
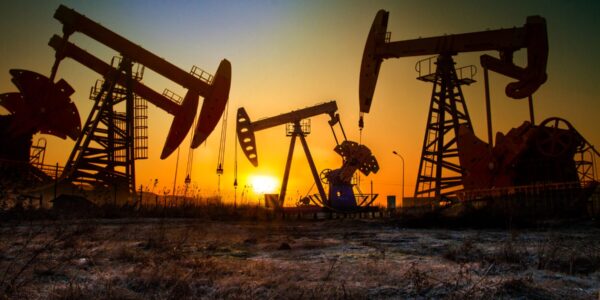
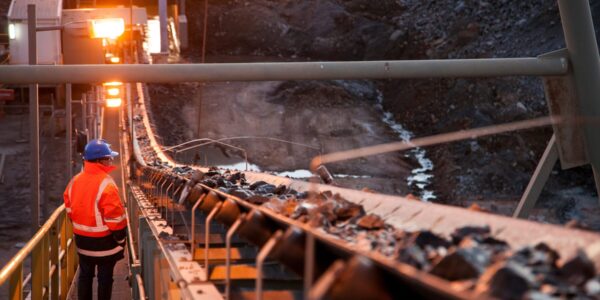
Many industries that we serve provide harsh conditions that lead to corrosion risks. Aggressive environments, extreme weather, damp settings and more can lead to materials corroding, and eventually damage or malfunction.
The industries we serve that present these challenges include:
- Pétrole et gaz
- Marin
- Nucléaire
- Pétrochimique
- Exploitation minière
- Agriculture
- Construction
- …and more!
Our Corrosion Resistant Metals
Corrosion resistance in a stainless steel or nickel alloy can provide superior performance and extend the working life of a product. Here come are suggested alloys for harsh environments, along with their chemical compositions.
Basic Austenitic Stainless Steel
304
CWI 304 [ UNS: S30400 / EURO: 1.4301 ] is a basic, austenitic stainless steel containing a minimum of 18% chromium and 8% nickel. This material meets the chemistry of the ASTM A580 specification.
316
L'acier inoxydable 316 de la série CWI est un acier inoxydable austénitique au chrome-nickel-molybdène avec une bonne résistance générale à la corrosion et une meilleure résistance aux piqûres.
UNS S31600 – Cr: 16.0-18.0%, Ni: 10.0 – 14.0%, Mo: 2.0-3.0% with full chemistry to ASTM A580
Duplex Stainless Steel
GEN 2209 is a filler material designed to weld duplex stainless steels such as UNS Number N31803. The welds are characterized by high tensile strength and improved resistance to stress corrosion cracking and pitting.
GEN 2594 provides matching chemistry and mechanical property characteristics to wrought superduplex alloys such as 2507 and Zeron 100, as well as to superduplex casting alloys (ASTM A890). Its structure results in high tensile/yield strength and superior resistance to SCC and pitting corrosion.
Advanced Austenitic Stainless Steel
904L
CWI Hi-Strength Series Stainless 904L is a low carbon, high alloy austenitic stainless steel designed for moderate to high corrosion resistance in a wide range of process environments.
UNS N08904 – Cr: 19.0%-23.0%, Mo: 4.0-5.0%, Ni: 23.0-28.0%, CU: 1.0-2.0%
Nickel-Based Alloys
La série de spécialités CWI Nickel Inconel 625 est un alliage à base de nickel utilisé pour sa haute résistance et sa résistance à la corrosion exceptionnelle.
UNS N06625 – Cr: 20.0-23.0%, Mo: 8.0-1.0% Ni: 58.0% min and Cb: 3.15-4.15%
CWI Nickel Specialty Series Inconel 825 is an austenitic nickel-iron-chromium alloy with addition of molybdenum and copper. It has excellent resistance to both reducing and oxidizing environments. UNS N08825 – Cr: 19.5-23.5%, Cu: 1.5-3.0%, Mo: 2.5-3.5%, Ni: 38.0-46.0% and Fe: Balance with full chemistry to ASTM B425
L'alliage CWI Specialty Series X750 est un alliage nickel-chrome durcissable par précipitation utilisé pour sa résistance à la corrosion et à l'oxydation à des températures allant jusqu'à 1300°F (704°C).
UNS N07750 – Al: 0.40-1.0%, Cb: 0.70-1.20%, Cr: 14.0-17.0%, Fe: 5.0-9.0%, Ni: 70% min and Ti: 2.25-2.75% with full chemistry to AMS 5698
La série C276 de Nickel Prime de CWI est un alliage nickel-molybdène-chrome renforcé avec une solution solide, avec une petite quantité de tungstène, qui présente une excellente résistance à la corrosion dans une large gamme d'environnements agressifs.
UNS N10276 – Cr: 14.5-16.5%, Fe: 4.0-7.0, Mo: 15.0-17.0% and balance Nickel, per ASTM B574
CWI Nickel Prime Series MP35N®* is a multi-phase, nickel-cobalt based alloy that has a unique combination of ultrahigh tensile strength, good toughness and excellent corrosion resistance.
UNS R30035 – Cr: 19.0-21.0%, Mo: 9.0-10.5%, Ni: 33.0-37.0% and Co: Balance per AMS 5844
The above alloys exhibit excellent corrosion resistance in a range of environments and should be considered for your next challenging application. For more information on our corrosion resistant alloys, and to kickstart your next project, don’t hesitate to reach out to our talented sales team at sales@centralwire.com.
Contactez-nous
Our team of experts is here to help obtain the required mechanical properties you need, and to advise how to further process the wire you purchase for your project every time. We aren’t just manufacturers, we’re industry experts who are here to make putting your project into action easy. Visit our website ici for full alloy lists and breakdowns, as well as helpful data sheets and more!
If you’re ready to invest in corrosion resistant materials to tackle your next project, Request a Quote with us today!