PROVIDING SPECIALIZED METALLURGICAL EXPERTISE
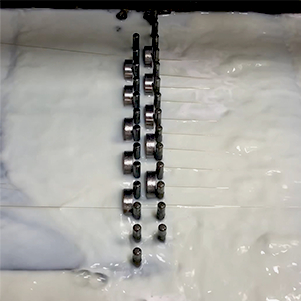
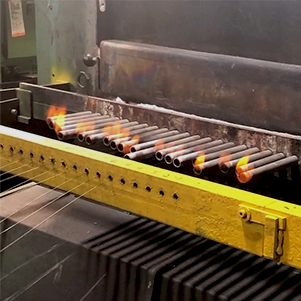
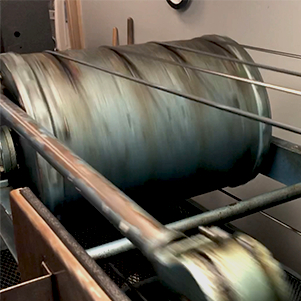
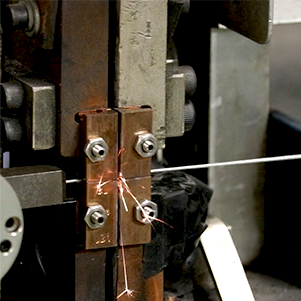
Rod Processing
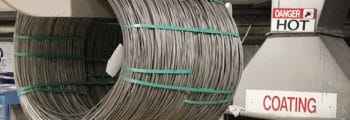
Incoming raw material (wire rod) is prepared for processing through a series of cleaning and/or surface treatment techniques, which include etching, pickling, and coating.
Rod breakdown
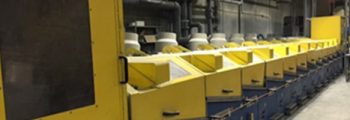
Wire mill rod coils with larger diameters are initially drawn down to sizes suitable for additional processing on equipment with small diameter output. Allows for multiple finished sizes to be drawn from an initial “redraw” size which in practice shortens lead times.
Annealing
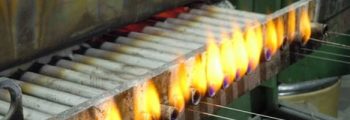
When the wire is drawn, it builds up strength due to work hardening. Time at temperature “softens” the wire and allows for continued processing or increased ductility or varied electrical properties in specific applications.
Stress Relieving
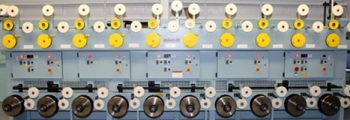
Particular wire alloys can be strengthened by “soaking” in a low-temperature bath. Also useful in strand and cable products where mechanical processes do not straighten effectively.
Dry Drawing
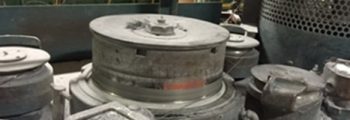
Processing wire in a dry lubricant to reach a desired diameter and tensile strength. Most common in larger diameters (above .040”) where surface area reductions are low and heat dissipation is not a primary concern. Creates a matte appearance of the surface finish which can be desirable for some aesthetic applications.
Wet Drawing
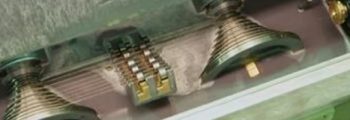
Processing wire in a liquid lubricant can be water or petroleum-based. Most common in smaller diameters where heat and penetration of the dies becomes a concern. Produces a shiny, smooth surface finish that is desirable in many applications — used primarily in finished diameters below .040”.
Fine Wire Drawing
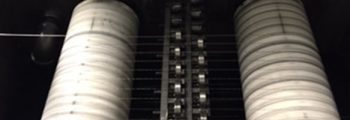
High-speed drawing of wire for critical applications with diameters in the 0.005” to 0.010” range requires specialized dies and drawing fluids to maximize strength and surface finish.
Cleaning
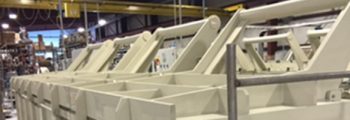
Aqueous acid wash or hot alkaline baths remove wire drawing lubricants to offer a cleaner material that extends furnace and lubricant life in downstream processing. Finished products are shipped that eliminate the need for additional cleaning before installation or further processing.
Coating
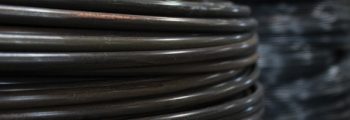
Wire is given a lubricating or preservative coating to assist with longevity or additional processing.
Straighten and Cut
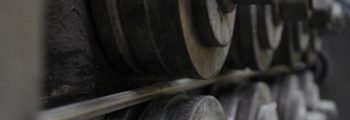
Coil product is converted to cut lengths as straightened bar stock. The straighten and cut bars are used in grinding, machining, shaping, and forming processes.
Center-less Grinding
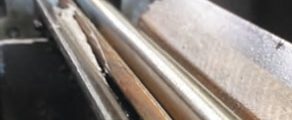
The through-feed center-less grinding process ensures high productivity up to .760”. The workpiece is fed through the grinding wheels completely, entering on one side and exiting on the opposite side. Material is bundled by individual lot to ensure full traceability back to the mill source.
Testing & Inspection
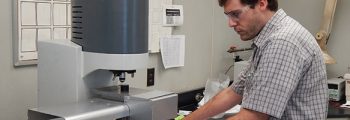
Strength, hardness, yield, conductivity, surface finish, and more are tested at various steps during the process to confirm 100% compliance with all specifications.
Spooling & Packaging
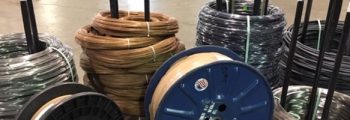
Processing bulk wire spools onto packages suitable for shipment. Labeling, marking, and kitting of the finished product. Customizable to any specification.