Applying Knowledge for Practical Solutions
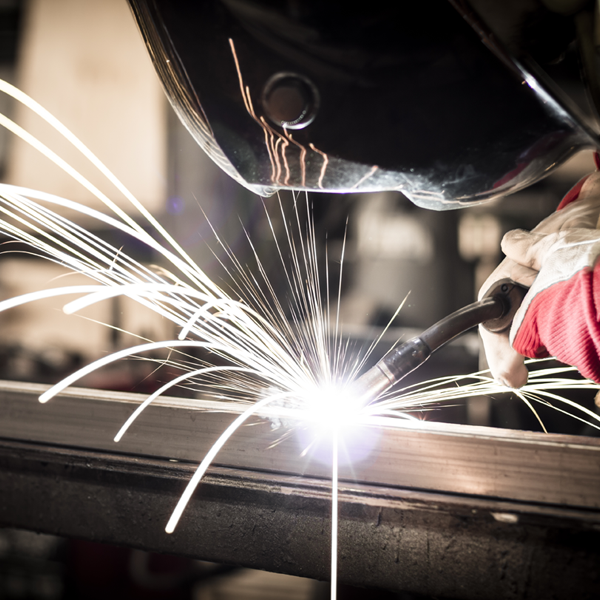
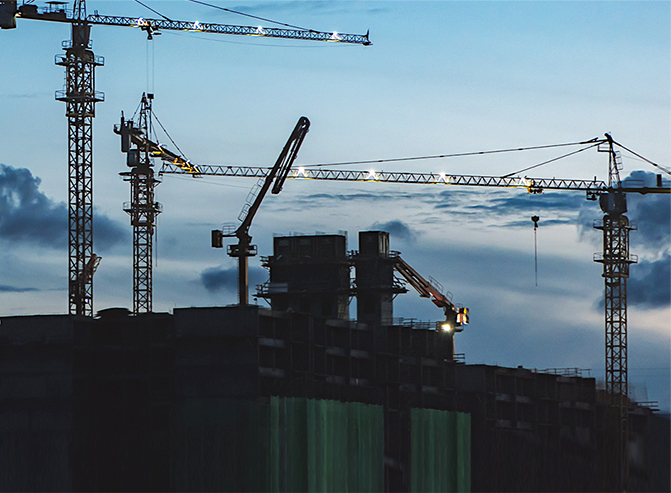
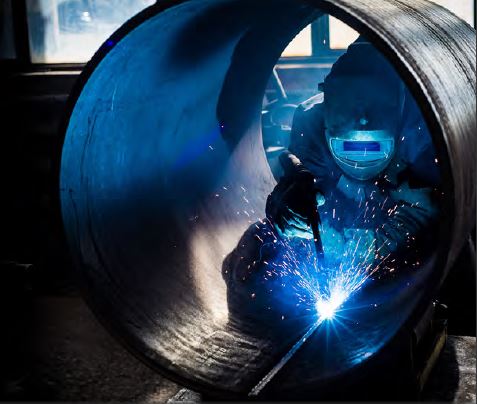
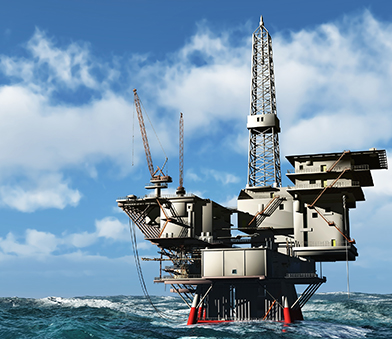
TANK FABRICATION
Containers for storage are commonplace is a range of industries. From fluid and gas storage in petrochemical processing to water and grain storage in food processing, welded tanks offer flexible solutions. Joining of corners, seams, and structural support allow for designs that can meet the specific volume, movement, and pressure requirements of a storage facility.
OVERLAY / CLADDING
CHEMICAL PROCESSING
PIPES
HYDRO TURBINES
High strength, advanced metals used in today’s power generation turbines require predictable performance and streamlined production, both of which are provided with the precision joining procedures available with modern welding alloys. Whether dissimilar metals are being overlaid to provide added functionality to blades, or similar metals are being joined to complete a housing or pipe viaduct, the welding of material gives Hydro Electric projects the flexibility and proven performance required to keep the lights on and the factories moving throughout the ever-connected world.