Years of experience and precision manufacturing capabilities support the high-performance and quality of our Tech-Mesh product line. Our Knitted Wire Mesh and custom Demister Pads serve various liquid-gas separation applications, from HVAC to Oil and Gas and more.
However, this product line is often mistaken for other, similarly functioning Mesh products such as Woven Mesh. Although both are a mesh product, the differences are plentiful, from the way they are manufactured to their end-use shapes and applications.
Today we will explore these differences and more, explaining the benefits to each product, and helping to determine what projects require each style of custom mesh.
Continue reading to further understand the difference between Woven Mesh and Knitted Wire Mesh, and where both products are commonly used.
Manufacturing Process
The manufacturing process of each mesh style involves meticulous precision in every step, to meet the requirements of robust applications. The Knitted Mesh process begins with rod processing and breakdown, preparing raw materials to maintain intended diameter and desired tensile strength.
The drawing and annealing processes follow, where further sizing is finalized, lubrication is done, and the mechanical properties of the mesh are crucially determined and finalized.
Finalized shape and construction are achieved through our knitting and crimping steps. Each individual wire is meticulously knitted together on our in-house designed knitting machine, where final properties such as rigidity, flexibility and strength are impacted. The crimping process creates pleats in individual sheets of mesh, to directly affect performance parameters such as removal efficiency and pressure drop.
Our final step is our support frame construction and attachment, which adds required durability to our mesh systems. These support frames are constructed from robust materials, typically matching the alloy of the mesh.

For the full step-by-step process in detail, check out our blog on how we turn Raw Materials into custom Tech-Mesh™ here!
The Woven Mesh manufacturing process differs from our Tech-Mesh™ process at the weaving stage, which replaces our knitting process. This step involves a wire loom set up with long lengths of wire strung parallel through the machine like yarn warp threads. The wires are then overlapped in an over-under weave to create the desired shape.
Design and Construction Differences
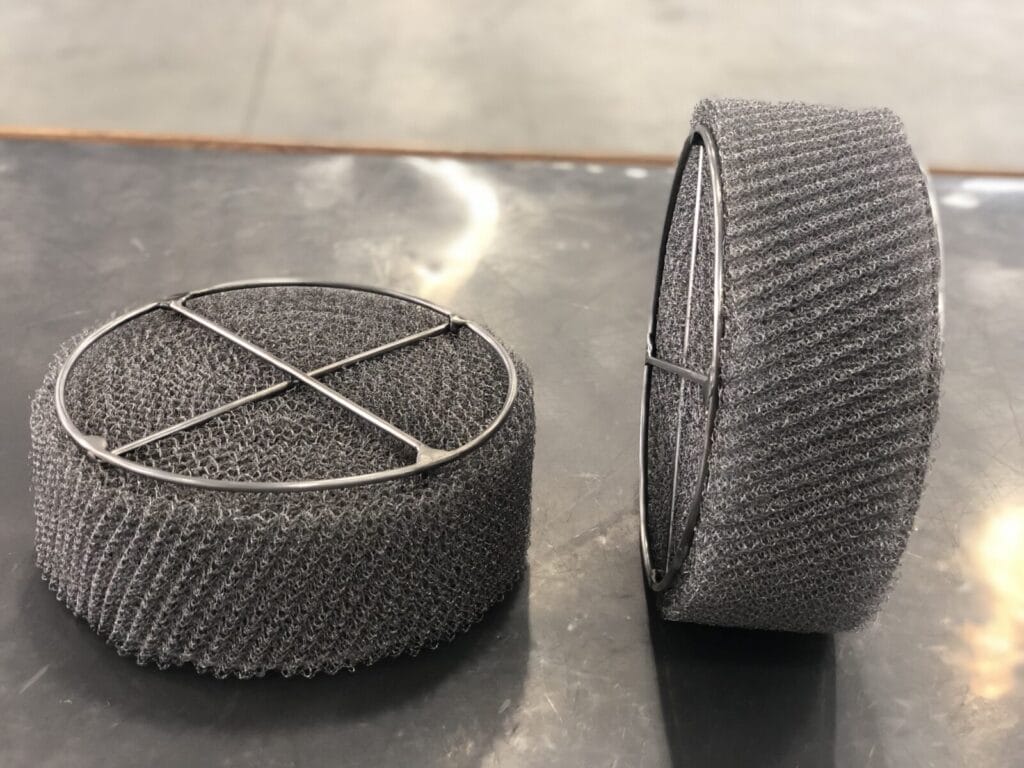
Both highly customizable, these products consist of different compositions that enhance their performance in their primary applications. Knitted Wire Mesh involves multiple sheets of mesh, dependent on the application. Customization is available when required for multiple mechanical properties, including:
- Mesh Density – Mesh Density customization and crimp style dictate the flow of liquid and gas through a mesh structure.
- Knitting Patterns – We have the ability to produce mesh in either open or tight patterns, depending on the separation requirements.
- Geometry – Fully customizable product geometry allows for application in a variety of vessel and tower shape applications.
- Support Frame – Support frame size and material options for any uses creating a strong, long-lasting connection between the Tech-Mesh™ and support frame.
- Flexibility and Strength – Material and mesh density options allow for mesh structures designed for extreme flexibility or added strength.
Woven Wire Mesh requires a slightly different final composition. Since it is woven with rigid wires, drawn to tight tolerances, the pore openings are relatively permanent and extremely precise. Knitted Wire Mesh is typically pliable, to aid in robust liquid-gas separation, while Woven Wire is intended to keep its exact shape. This gives it a more durable screening ability, although the manufacturing process of Knitted Wire Mesh offers far fewer customization limitations.
Common Applications
The final construction and manufacturing process of these two mesh styles cater to different end-use applications. The most common applications for Woven and Knitted Wire Mesh include:
Woven Wire Mesh:
- Strainers
- Woven Wire Baskets
- Electrical Shielding
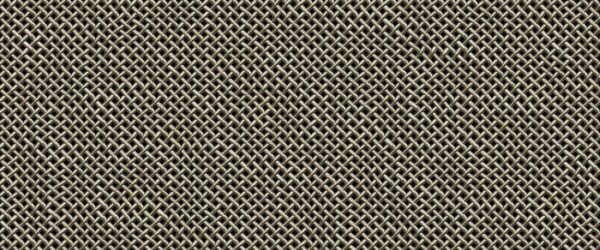

Malla metálica de punto
- Refinery Towers
- Brewing and Distillation Equipment
- Pollution Control Equipment
- Knockout Drums and Receivers
Mesh Capabilities at Central Wire
At Central Wire, we manufacture custom Knitted Wire Mesh domestically in both Canada and the United States. Our capabilities allow us to Bulk Mesh and Custom Demister Pads in a wide variety of wire diameters, alloys, mesh densities and more from various raw materials.
Although we do not manufacture end-use Woven Wire Mesh, our high-quality Fine Wire is commonly used in its manufacturing process. With the ability to produce sizes from 0.001” up to .032”, with tempers ranging from soft annealed to spring temper, we can provide the product for your exact specifications, available in Stainless, Nickel, Copper and Specialty alloys.
Unmatched Quality and Precision: A Trusted Mesh Supplier
Investing in Central Wire means choosing a trusted global supplier of precision products, manufactured with premium raw materials. Our Knitted Wire Mesh products provide critical solutions relied on by Oil and Gas corporations, Breweries, Distilleries, and countless other companies.
Our high-quality Fine Wire across Medical, Aerospace and Commercial industries in various applications, and provides precise performance when used in the manufacturing of Woven Wire Mesh.
To unlock the potential of our quality-tested, industry trusted products, Request a quick and easy Quote with us below!