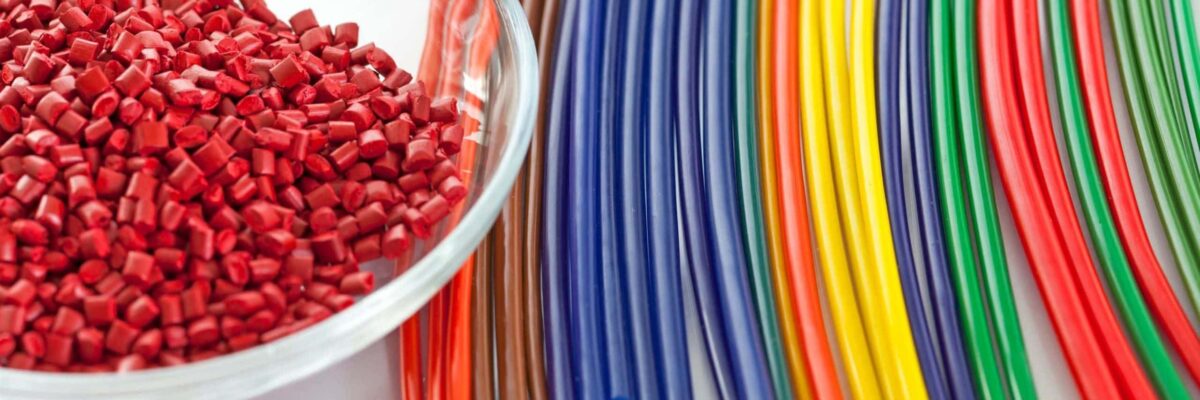
What is Coated Cable?
Coated cable is typically wire rope, aircraft cable, or bare cable that has been covered in another material like Poly-Vinyl-Chloride (PVC), Nylon, or Polyethylene. The coating creates a sheath around the cable, adding additional protection to the strands. The extruded coating also increases abrasion and rust resistance, allows for customization of color, and increases safety for low light applications.
What is the purpose of coating cable? On top of the protection benefits that it has, coated cable can have better weatherability than bare cable. The plastic coating can help protect the cable in environments where extreme temperatures and weather are present. Covering the cable with a coating helps it last longer by protecting it from direct contact with the environment. This barrier prevents damage and extends the cable’s lifespan.
How is it Made?
Coated cable starts with bare aircraft cable or wire rope and the chosen extrusion material. Most extrusion materials start as resin pellets. The operator feeds the pellets into the extrusion machine and slowly heats them until they reach their melting point.
As the resin is melted, it is pushed through the crosshead with a feed screw. The cable enters the backside of the crosshead where a wire guide is used to help maintain the centering of the cable. The cable picks up the molten resin as it passes through the crosshead and leaves through a coater die which controls the diameter and profile of the coated cable. The cable is then cooled through a series of water troughs. The extrusion machine has varying settings and parameters, allowing customers to get the exact coating needed for their application.
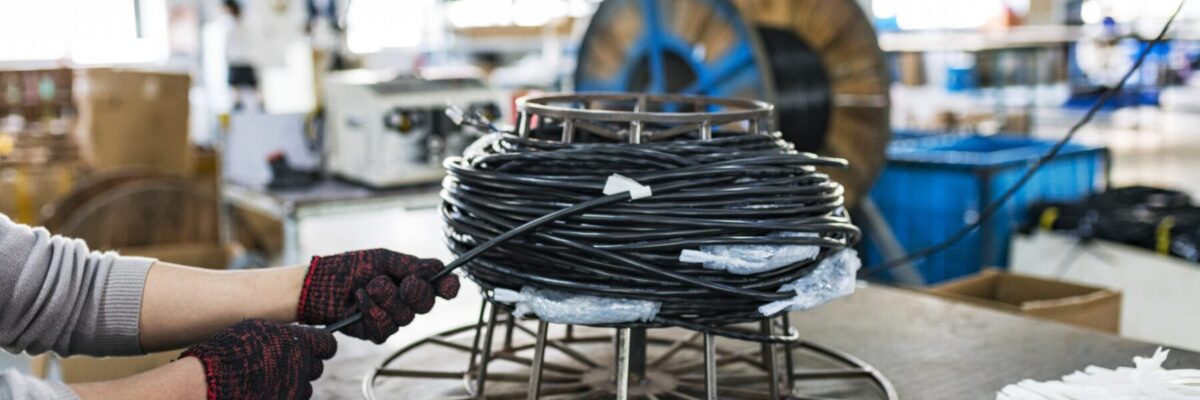
Common Coating Types
Poly-Vinyl-Chloride (PVC), Polyethelyne (PE), and Nylon are the most common coating types utilized in the manufacturing of Coated/Extruded Cables. Each coating type provides a specific integrity characteristic particular to the end-use application. Loos&Co. and Sanlo have an extensive history in the Coated Cable market, allowing us to give customers the knowledge and understanding that they need to make the best material selection.
Poly-Vinyl-Chloride (PVC):
PVC is the most commonly used plastic for mechanical cable coatings. The main reason for PVC’s popularity is it has a relatively low cost. The primary material that determines the majority of PVC’s capabilities is vinyl.
Vinyl is flexible and has good weathering resistance. A feature that separates vinyl from many other plastics is its ability to withstand the sun’s ultraviolet rays. The operating temperature of vinyl is between -30°F and +180°F. The other main benefit of choosing PVC is its general use abilities. Vinyl is available in a wide range of hardness and durometers, from extremely soft and spongy to extremely hard and stiff. PVC offers a lot of manufacturing flexibility, so many industries use it.
Polyethylene (PE):
PE is primarily used as an electrical insulation plastic. Similar to PVC, PE is a very popular cable coating option because of its relatively low consumer cost. The plastic is quite flexible in thin wall thickness, and in heavy wall thickness, it is stiff. The operating temperature range for PE is between -40°F and +200°F. While PE does have good resistance to chemicals and weathering, it has little abrasion resistance ability.
Due to PE’s lack of abrasion resistance, it is not commonly used on the outside jacket of a mechanical cable. PE’s best use is as an insulation material in electromechanical cables.
Nylon:
Nylon is used heavily for mechanical cable applications. It has excellent abrasion resistance which helps prevent push-pull actions that can cause damage to the cable overtime. It offers superior protection when subjected to abrasive mechanical movements.
Nylon also has excellent UV protection because it contains UV inhibitors. This allows Nylon to be used in outdoor applications with limited damage caused by UV rays. The operating temperature for Nylon should not exceed 180°F, limiting the applications where Nylon coated cable can be used.
Due to Nylon’s excellent abrasion and protection qualities, it can increase cable life by 2 to 3 times the standard lifetime in most applications. This plastic can also be easily colored to suit your specific application needs.
After understanding the differences between these three common types of plastic, you are sure to choose the correct coated cable for your needs!
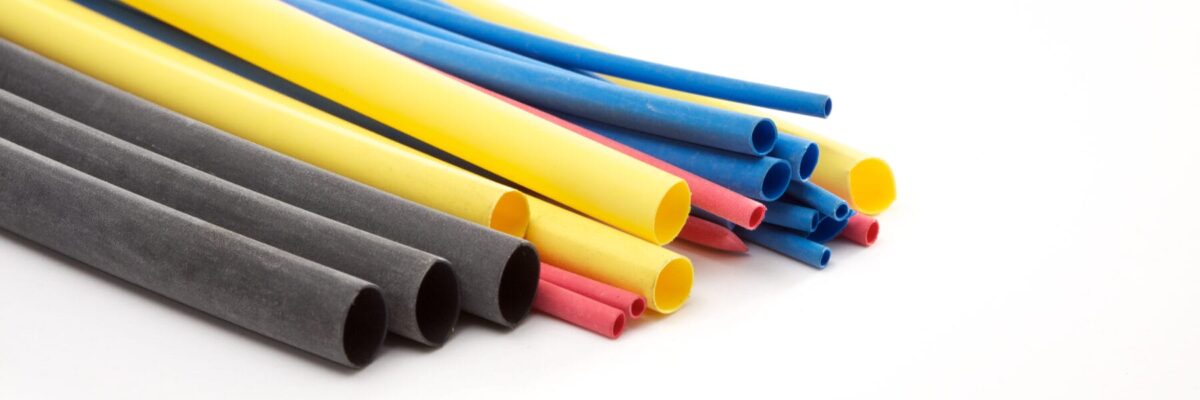
Where are Coated Cables Used?
Various industries use coated cables in a variety of applications. Some of the most common applications include:
- Brake and release cables
- Fish tapes
- Cable railings
- Bike lock cable
- Lock out tag out cable
- Conveyor cables
- Aircraft cables
- Architectural cables
- Door restraint/closure
- Fitness cable
- Mooring cable
Coated cables serve a multitude of purposes, from safety measures to mechanical cables, depending on their application. No matter where you need coated cable, Loos &Co. & Sanlo can help! We have the experience, capabilities, and expertise to manufacture coated cable for any application.
How do our capabilities cover the full scope of the Coated Cable Market?
As experts in the manufacturing of Coated Cable, we have developed several innovative product lines that help to ensure our expertise and capabilities benefit all in the Coated Cable market segment.
Our innovative Coated Cable Products include:
Reflexlite®
Reflexlite® is reflective wire rope that is designed to enhance low light or nighttime visibility where delineation is needed to see hazardous objects or situations – ideal for mining shafts or tunnels, low-light roadway infrastructure, low-light rescues or general marking.
Canveyor® Conveyor Cable
Canveyor® Conveyor Cable is the perfect coated cable solution for industries requiring high abrasion resistant conveyor cable. Some of the segments that Canveyor® is ideal for: Packaging and Distribution Warehouses, Food Processing, Medical Technologies and Laboratories.
Exerflex® Fitness Cable
Exerflex® Fitness Cable is perfect for Fitness Equipment Manufacturers, Gym Owners, Fitness Equipment Repair Specialists, who are looking for an abrasion resistant fitness cable that last longer and holds its integrity, therefore reducing repairs, downtime and risk of injury due to failing equipment.
Mooring & Oceanographic Cable
Our Mooring and Oceanographic Cable is trusted in a variety of offshore applications. Manufactured with a spin and corrosion resistant design that is perfect for maintaining buoyed monitoring equipment and data collection devises in environments ranging from warm and tropical (Gulf of Mexico and the Indian Ocean) to cold and unforgiving (North Pacific and the Great Lakes).
No matter where you need coated cable, Loos & Co. and Sanlo can assist in getting you the product you require. Start your coated cable project today, call us, 1 (800) 533-5667, or visit our website.
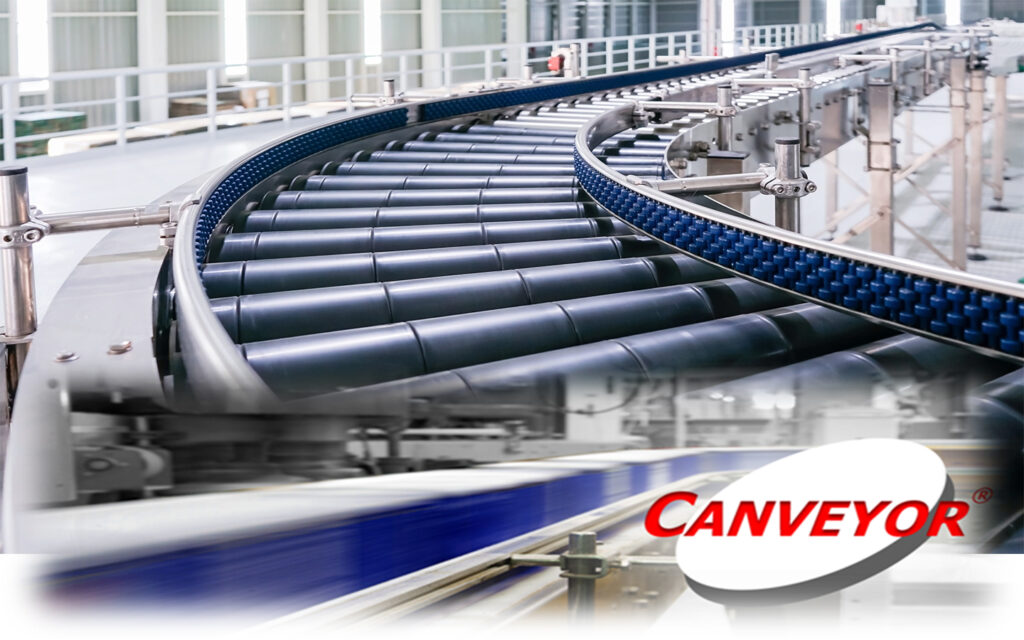
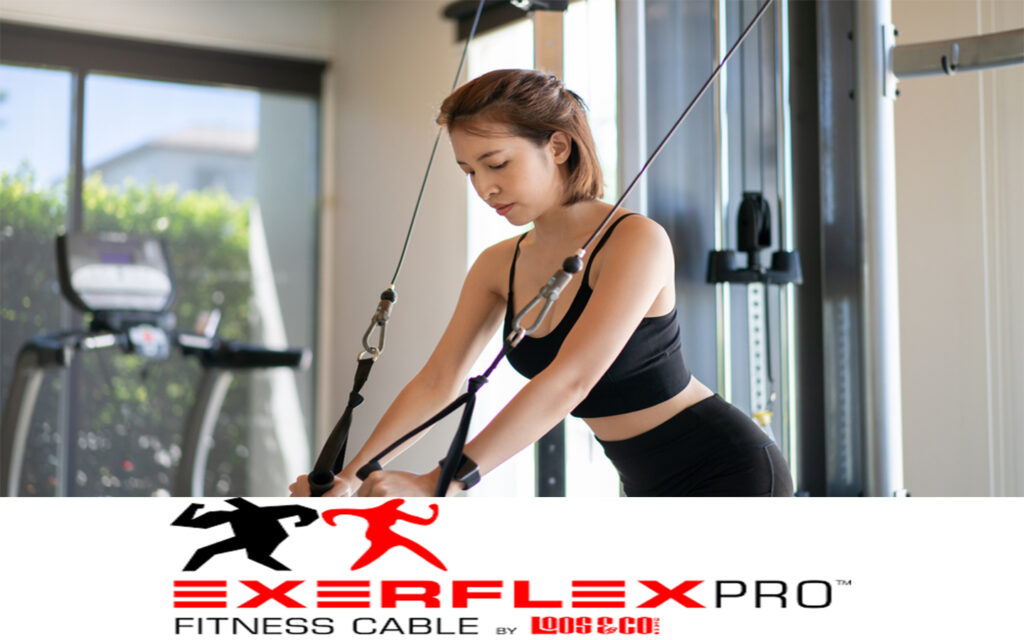

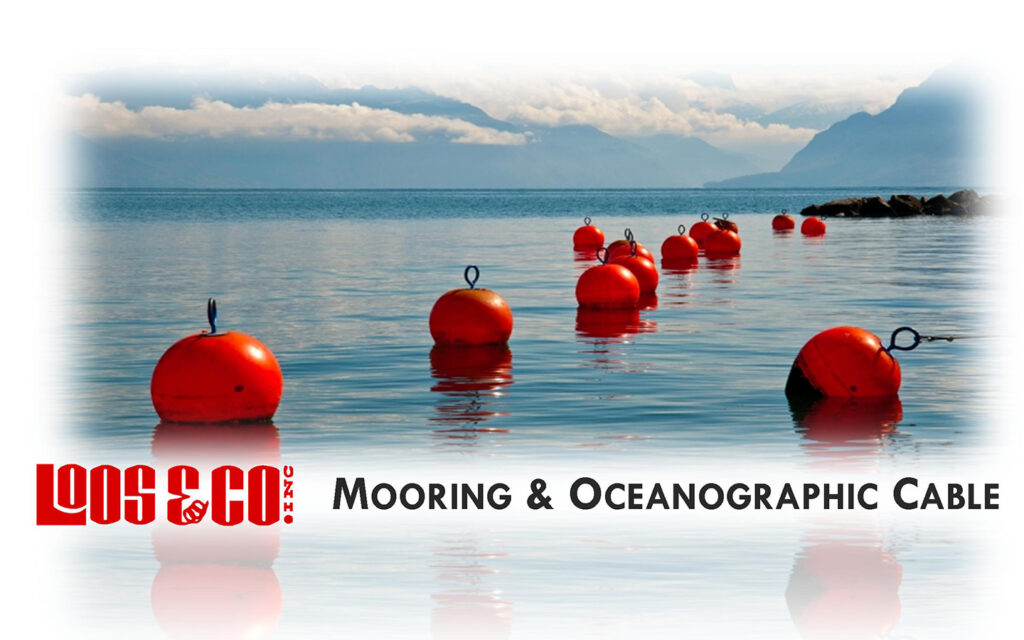