Many of the applications of our Alambre en forma products demand high levels of corrosion and oxidation resistance, as well as strength. Even some of our Premium alloys need an extra boost of strength to perform in Mines, Oil and Gas Refineries, and Marine applications. This is where precipitation hardening, a common procedure used to make materials even more durable and dependable, comes into play.
Precipitation hardening is a heat treatment process which increases the tensile strength and hardness of various alloy families. In some cases, this process can increase the yield strength of an alloy fivefold.
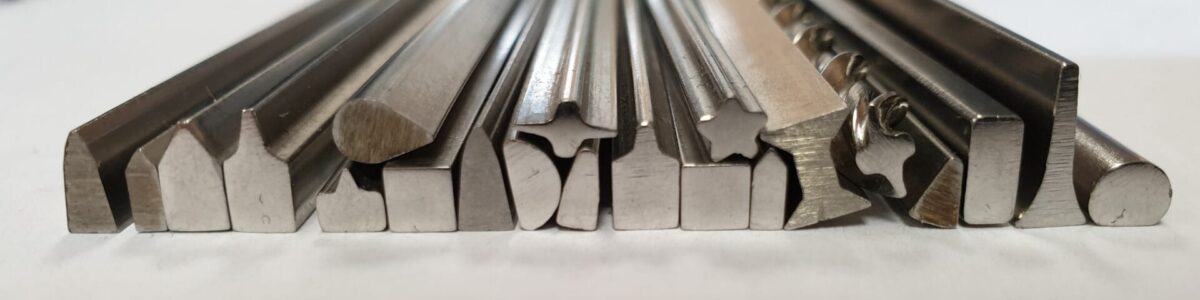
Precipitation Hardening with Inconel® X-750
As part of our Specialty Series Alloys, X-750 is a corrosion and oxidation resistant nickel-chromium alloy, which is also heat tolerant at temperatures of up to 1300°F. It is ideal for use in extreme, high temperature applications that would normally cause issues with most materials, because it is precipitation hardened for superior performance.
The multi-step process changes the physical structure of the metal and allows it to be stronger and more durable than before. Let’s take a look at how this process works, and why it is so successful in strengthening and adding durability to premium alloys.
The Precipitation Hardening Process
Precipitation hardening uses temperature and time control to improve the mechanical properties of the alloy. Typically, the precipitation hardening process consists of three steps: solution annealing, quenching and aging. Let’s take a dive into how each step helps reinforce premium metal alloys.
Solution Annealing (Sometimes Called Dissolution)
The first step of precipitation hardening involves heating the alloy to a temperature just below its melting point. Before this, a constituent metal is added to the main material. This is an additional material which will improve the properties of the alloy.
This high temperature is called the “solvus temperature” and this helps to dissolve grains of impurities that have been added to the main material. It is the temperature at which you can dissolve the most amount of a solid in a solution. The mixture sits at this temperature for a certain amount of time depending on the material, in a stage known as soaking.
Quenching
Once the dissolution of all impurities is complete, the alloy will be rapidly cooled back to room temperature. This “quenching” technique enables us to trap the new saturated solution in a metastable phase.
Achieving this phase without most of the new solute precipitating out of the solution is only possible with rapid cooling. A slow cooling process would typically undo most of the work from the solution annealing step. The material at the end of this step is a soft solid solution, with relatively low strength.
Ageing
In the third and final stage, the solution is heated again, but not to as high of a temperature as step one. The elevated temperature begins what is called precipitate formation. Fine precipitates develop in the solution and form large strain fields in it which enhance breaking strength and hardness of the final product.
Depending on the materials used, ageing can also occur at room temperature, and that process is called natural ageing.
As time passes, with exact timing depending on the material, it will reach a peak value of hardness. At this point the strength, corrosion resistance and ductility are at the highest they can be. Overaged materials will slowly lose these qualities.
What Industries Use Precipitation Hardened Materials?
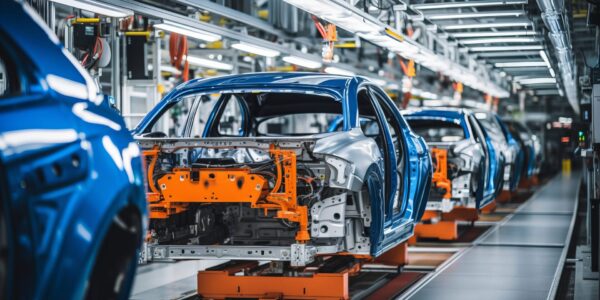
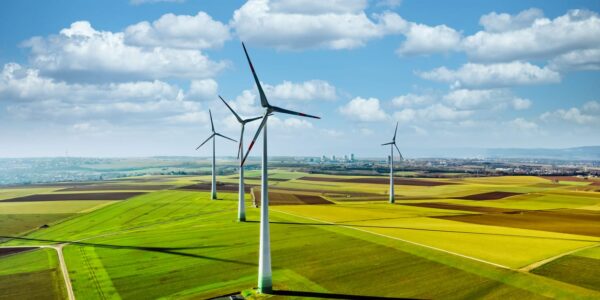
Industries with high demands for temperature resistant, corrosion resistant, strong and durable materials may need alloys that have been precipitation hardened. The breaking strength and resistance to hazards of these upgraded alloys allows for peak performance without concerns of wear and tear or malfunction.
The conditions of industries such as Aerospace, Automotive, Renewable Energy, Oil and Gas, Marine and more can require precipitation hardened materials for their excellent strength to weight ratio, and resistant to corrosion and intense temperature changes.
CWI Products with Precipitation Hardening
In terms of our product lines, specialized alloys such as Inconel® X-750 go through this process to earn their name as a superalloy. Its versatility and durability are unmatched and makes it an excellent option in many industries. Other alloys that can be precipitation hardened for high temperatures and toxic environments include Inconel® 718 and Monel® K500, both of which are nickel-based.
In terms of end-use application, small components such as gears, shafts, engine parts, fasteners and turbine blades are often precipitation hardened to withstand heavy loads and toxic environments. In cars, planes, turbines and more, these small components require strength-to-weight ratios to handle the repeated use and heavy loads these industries cause, whilst keeping the structures lightweight.
Choosing Premium Alloys at Central Wire
At Central Wire, we prioritize innovation in manufacturing premium alloys for challenging industry conditions. For a full list of our manufactured material options, check out our comprehensive alloy page here!.
If you want to learn more about X-750 and its capabilities, chemical composition and more, we have an alloy specific page for it on our site too!
If you’re ready to invest in the premium alloys we provide for your next project, Request a Quote with us today!