At Central Wire Group of Companies, we proudly boast AS9100 certification that allows us to serve the mission critical industry of Aerospace. Il nostro MIL-spec products are trusted to perform through the harsh conditions that aircraft applications may produce. In this blog, we will focus on some of the most important qualities of our Aircraft Cable products.
The long list of unique challenges in this industry include drastic altitude and weather changes, risks of corrosion and the responsibility of keeping passengers and cargo safe. Avoiding wear and tear on Aircraft Cable takes quality materials and knowledgeable manufacturing.
The Aerospace applications that use our Aircraft Cable are essential, from flight control to emergency control systems. As industry leaders, we understand the importance of quality, durable cables to adhere to these applications.
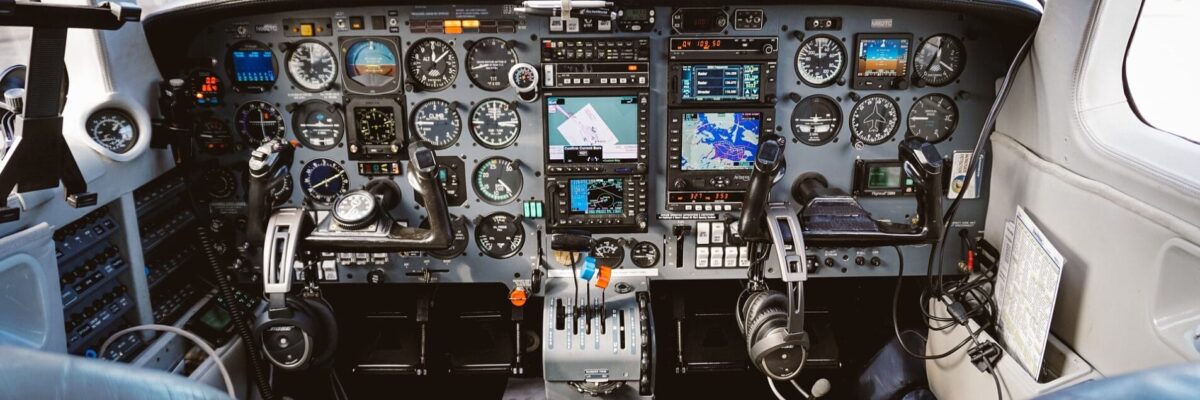
Characteristics to Consider
Aircraft Cable works like a machine, wherein the characteristics of strength, flexibility, and fatigue work together to create balance. Modifying one characteristic inherently impacts the other two, and these changes influence the cable construction, functionality, and performance of a cable.
When determining the correct Aircraft Cable for your application, or comparing different cable configurations, it is essential to understand how these factors work together to create a product that is flexible when it needs to be, and strong when it matters the most.
Flexibility
In general, the more wires or strands a cable has per a given diameter, the more flexible it is. The more flexible it is, the less quickly it fatigues through repeated bending. In applications like flight control, repeated use and bending is required for a pilot to keep control of the plane, so flexibility of cables becomes a focus.
What is the Difference Between 7x19 and 1x7 Strand?
Comparatively, cables with fewer wires or strands offer greater strength, but with a lesser tolerance to fatigue, and they are typically less flexible. 7×19 Aircraft Cable, for example, is extremely flexible compared to 1×7 strand, and 1×7 is more susceptible to the effects of bending.
Strength
Aircraft Cable that is correctly specified for an application should possess abrasion resistance, be able to withstand repeated bending, as well as other forms of stress. 1×7, 7×7, 1×19, 7×19, and 19×7 cables are all configured to excel in different applications given their corresponding configurations, diameters, and break strengths; and while a certain cable may be appropriate for one application, it may not be the best choice for another.
Why Would you Choose 1x7 Strand?
In general, lower wire or strand counts result in a higher strength cable. Let’s compare 7×19 cable to 1×7 strand again. 7×19 Aircraft Cable performs well when flexibility and fatigue are concerns, which is why it is used commonly in winches and garage doors, yet it is not as strong as 1×7 strand, which has a higher breaking strength and performs best in standard rigging, structural supports, and push-pull applications.
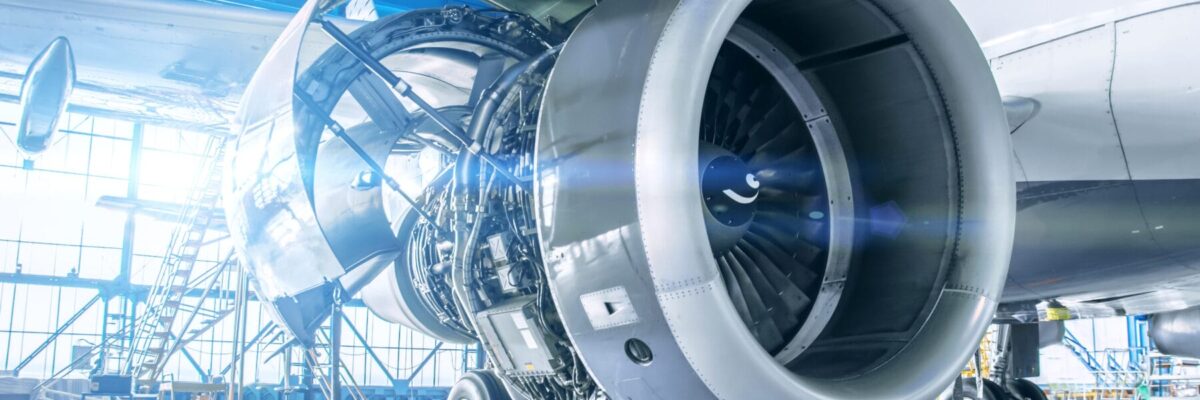
Fatigue
Cable fatigue is triggered by small cracks in the wires because of repeated bending and straightening over sheaves or drums. Often referred to as the cable’s cycle life, this wear is inevitable with time but can be delayed by employing appropriately sized sheaves, ensuring the cable is appropriately lubricated, and limiting the number of different directions a cable bends.
- Sheaves: In general, larger sheaves are a more effective choice for larger cables, faster operating speeds, and heavier loads, because large cables with small sheaves typically accelerate damage. Smaller sheaves can be used without causing early stress if the operating speed is slow, the cable is smaller, or the loads are lighter.
- Lubrication: Aircraft Cable is lubricated to reduce friction and provide protection against corrosion. Corrosion and abrasive wear can shorten the cycle life of a cable, especially when the cable travels around sheaves.
- Bend directions: It is best practice to avoid reverse bends whenever possible. Reverse bends, where a cable bends in one direction and then the opposite direction, can expedite damage and reduce the lifespan of a cable. If reverse bends are unavoidable, larger sheaves and thicker cables will offer a longer cycle life.
Investing in our Aircraft Cable
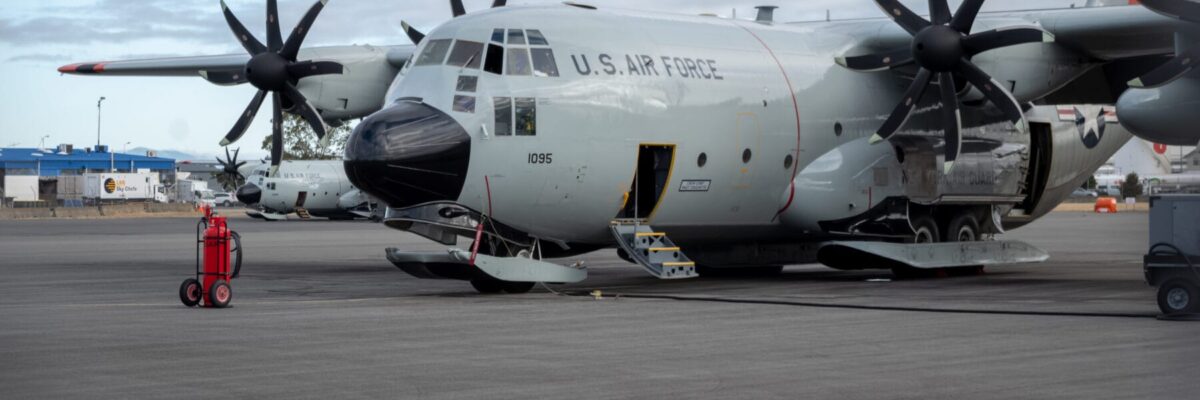
For projects in the sky, we have all the products you need. We manufacture our Aircraft Cable with materials including stainless steel, galvanized and specialty alloys. Visit our product page qui to learn more about material options
With strand sizing options ranging from 1×7 to 7×19, we have got you covered for whatever mission critical application you can think of. If you’ve still got any questions about our Aircraft Cable products, reach out to our expert sales team for more information at sales@loosco.com.
If you’re ready to invest in our Aerospace products, request a quote with us today!