In mission critical industries like Aerospaziale, Gruppi di cavi are subjected to a relentless stream of stresses that create risks of malfunction. These challenges not only highlight the complexities of Aerospace engineering and manufacturing but also emphasize the critical role Cable Assemblies play in ensuring safety and performance in aviation.
These challenges put importance on material and supplier choices, as only the top-quality materials can excel in aircraft applications. Choosing the right materials from a trusted supplier that is certified to the industry standards can prevent product malfunction and ensure consistent performance in flight control, emergency systems, and more.
This blog will highlight three of the predominant challenges facing Cable Assemblies in this industry, and why choosing the precision manufacturing and industry knowledge of Loos and Company is the right choice every time.
Industry Challenges
When it comes to the intricate world of Aircraft Cable Assemblies, the challenges faced are both diverse and demanding. Let’s dive into the top three challenges that require precision, innovation, and strict adherence to industry standards.
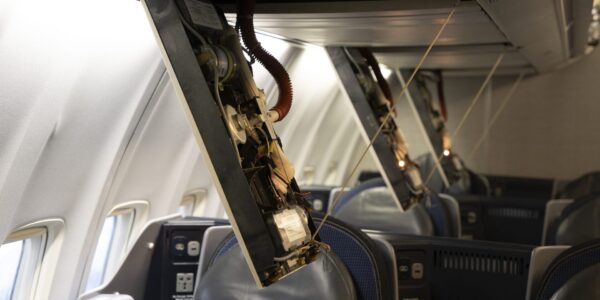
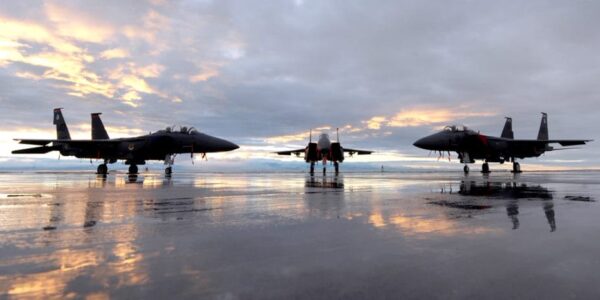
Lifespan and Fatigue:
In Aerospace applications, Cable Assemblies can be subjected to extreme temperatures, vibrations, and tension. Over time, these factors can lead to a phenomenon known as cable fatigue. This wear and tear is measured in terms of time or cycles, with rigorous physical tests ensuring that cables maintain a high threshold for fatigue degradation.
The aircraft’s constant exposure to atmospheric conditions further accelerates fatigue. This continuous battle against environmental stressors underscores the need for routine maintenance and inspection to prolong an aircraft’s lifespan and ensure its safety.
As industry experts at Loos and Company, we understand the engineering that goes into preventing cable fatigue and malfunction. We have full quality control from start to finish in our AS9100 certified plants, as we manufacture both the Cable and Fittings for our Assemblies. The high breaking strengths of our Cables, along with galvanized, stainless steel, and other material options ensure you can trust our products to perform through these environmental concerns.
Proper Cable Selection:

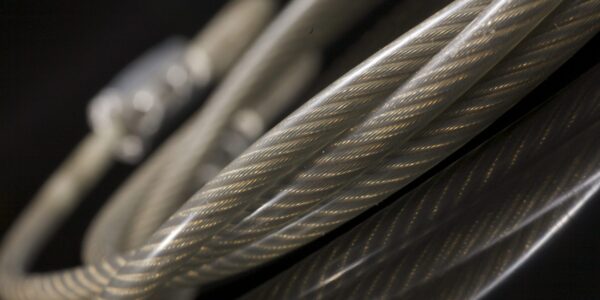
Our innovation and manufacturing capabilities provide a variety of options to our customers, from cable size and construction to different materials and coating options. In Aerospace, these are pivotal decisions that are specific to the requirements of each application. The process demands meticulous evaluation, and the consideration of many factors, as the repercussions can affect both the safety and performance of an aircraft.
The weight and breaking strength of a cable are cornerstones of this selection process. A cable’s load-bearing capacity is a crucial element in Aerospace applications where safety is crucial. However, some intricate applications may require a lightweight option that possesses a good strength-to-weight ratio. Regardless of the specific application, Aerospace assemblies must have the strength and ability to withstand repeated use to avoid costly malfunctions.
Aerospace applications may involve exposure to harsh environmental conditions, including corrosion risks and varying weather conditions. Thus, cables need to exhibit robust corrosion resistance to ensure their long-term reliability and the safety of the aircraft. In the complex landscape of Aerospace cable selection, the interplay between these factors shapes the decisions that drive innovation and safety in the industry.
Thankfully, our industry knowledge allows us to prepare for these challenges. With cables possessing breaking strengths of up to 50,000 pounds, and corrosion resistant materials like 302/304 stainless steel, Loos & Co. Cable and Assemblies can withstand the harsh environments of the Aerospace industry.
Selecting the Correct End Terminations:
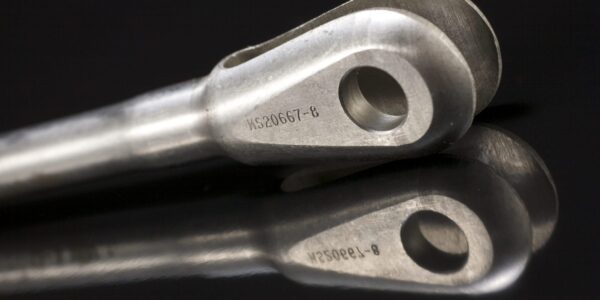
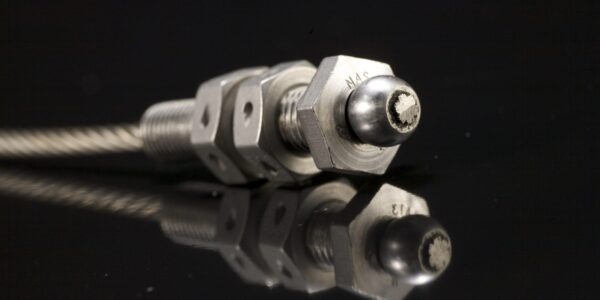
Choosing the right end terminations isn’t just a matter of preference; it’s a must. These terminations must align perfectly with their intended purpose to ensure smooth operation.
Mismatched terminations can be compared to using the wrong tool for a job, causing significant problems and, in the worst cases, safety risks. In the Aerospace industry, where precision and safety are critical, the careful selection of end terminations is non-negotiable. This process guarantees the reliability and safety of Aerospace Cable Assemblies.
At Loos, our Hardware and Fitting capabilities are endless, possessing the capabilities to meet the specifications of any Assembly needs. Our Ball Ends, Fork Ends, Eye Ends, Stamped Eye Terminals and other end terminations are all capable of consistent performance and strength in demanding Aerospace industry conditions.
Why Rely on Loos & Company for Aerospace Assemblies
In the dynamic industry of Aerospace, combining aircraft cables and terminals must be carried out by a qualified manufacturer in strict adherence to specific industry regulations and standards.
Loos & Co. takes pride in meeting and exceeding the highest levels of qualification, quality control, and testing required in the Aerospace industry. Backed by prestigious certifications such as AS9100:D, ISO 9001:2015, and ISO 13485:2016, we ensure the highest standards of quality and safety. When you choose Loos & Co., you are choosing excellence, trust, and a future dedicated to innovation and precision.
If you’re ready to invest in our innovative and vast Cable Assembly capabilities, Request a Quote with us today!