Corroding, cracking, or kinking Slicklines are a recipe for failure in any downhole project. Damaged wire lines can cause delays in logging and production, or worse, potentially result in broken lines, lost tools, or even injuries to the crew.
The durability of your slicklines, whether they be for Oil, Gas, or Geothermal production, matters to you, and the profitability of your well. Safe and effective energy production starts with durable slicklines.
Why Are Quality Slicklines Important?
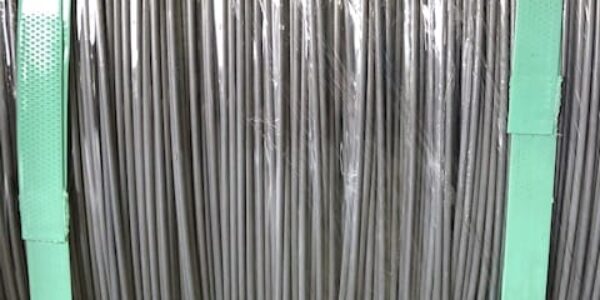
Quality Slicklines:
- Protect from Wire Failure
- Save Valuable Downtime
- Keep Projects & Jobsites Safe
Continue reading below to learn what separates Central Wire GD™-SUPA Slicklines from the competition and makes them the right choice for your downhole applications every time.
Industry Challenges
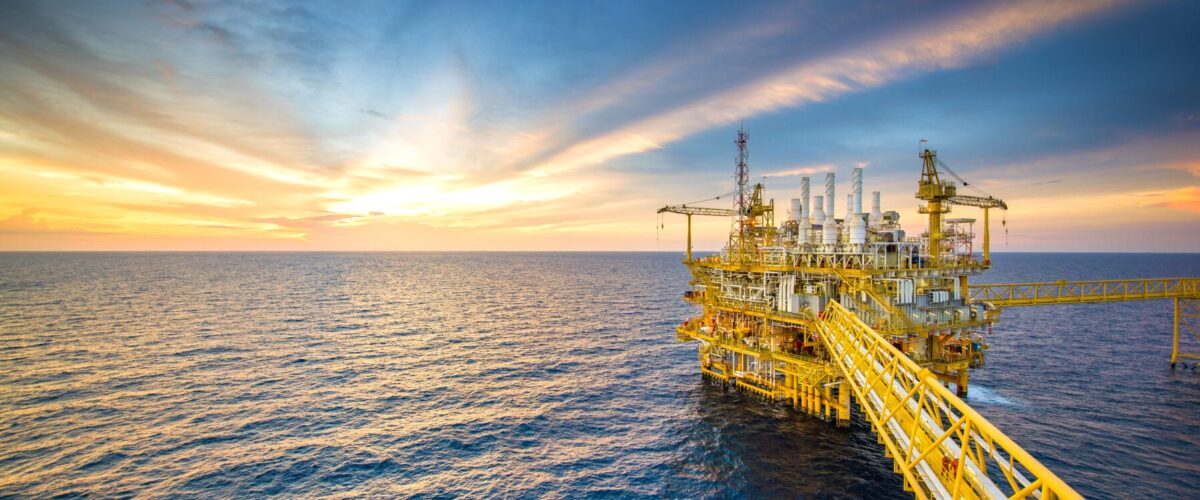
The industries served by Slickline products offer unique challenges that put materials through harsh conditions. Here are a few of the conditions which make downhole environments demanding:
Corrosion Risks
- Risks of corrosion are extremely common in Oil and Gas, and Geothermal plants. The relatively toxic environments can cause damage to various materials.
- These plants can be both “sour” and “sweet” environments. “Sweet” environments have very little hydrogen sulfide and are less hazardous. “Sour” environments are high in H₂S, which is a toxic and corrosive gas.
Variety of Environments
- Slicklines are manufactured to function on-shore and off-shore, which offer different environmental challenges such as saltwater corrosion risks off-shore.
- Being in mostly outdoor and downhole environments leads to different temperatures, and Slicklines must be able to handle these rapidly changing conditions.
Safety Risks
- Working with Slickline equipment involves safety risks related to equipment failure, accidental release of well fluids or high-pressure conditions. Quality testing for these products is crucial to ensuring safety in these plants.
GD™-SUPA Slickline Alloys
Our line of GD™-SUPA Slicklines features eleven different Alloy options, ensuring the perfect product for your project. The material variety includes austenitic Stainless Steel, duplex Stainless Steel, and more materials suitable for toxic well environments.
The high breaking loads and resistance to corrosion, as well as toxins like phosphoric acids, make these alloys ideal for demanding conditions in these industries.
If you want to know more about our Alloy options, their chemical compositions and other qualities, check out our Slickline Alloy Summary Sheet here.
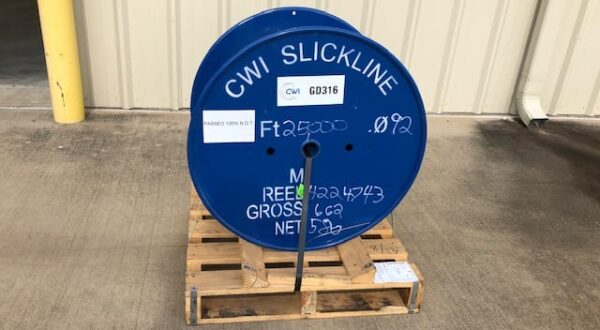
Maintenance and How to Maximize Your Slickline Life
Along with choosing the right material, good maintenance helps guarantee long operating lives for manufactured materials. To maximize the life of your Slickline, we suggest following these guidelines:
- Confirming that the wire is suitable for your expected well conditions. Our experts would be happy to help you figure this out.
- Use new packing in the stuffing box and change the wire guides if they show signs of excessive wear.
- Use correct sized sheaves (rule of thumb – sheave diameter = 120 x wire OD.)
- Always lubricate the wire when running into the well.
- Never exceed the maximum allowed wire tension. This will be set at a maximum of 60% of the breaking load reported on your CWI issued test certification.
- Clean the wire pulled from the well; use a wireline wiper to remove well fluids.
- Always update the wire logbook with the wire-cut off and data from the operation.
EN10204 Standards
At Central Wire, we pride ourselves on quality that you can trust. This means industry compliance and manufacturing certifications that prove our reliability.
Each Slickline comes with a certificate of conformance that states physical and mechanical properties, including alloy chemistry and breaking load. Every line can also be verified by an independent lab to EN10204 standards.
These standards help ensure that the materials used in products meet certain quality standards. For our Slicklines, they can be tested inspected to confirm quality, accuracy and durability that confirm the product can handle harsh conditions.
Contatto
As industry leaders in Slickline manufacturing, we understand what it takes to produce a product that customers can rely on. Our expertise and industry standard compliance make us your trusted source for downhole products.
With eight material alternatives to choose from, our GD™-SUPA Slicklines can handle the harshest of industry conditions both on-shore and off-shore. If you have any questions about our alloy options and which is right for you, contact our knowledgeable sales team at [email protected]
If you’re ready to invest in our Slicklines to maximize the efficiency of your downhole operations, Request a Quote with us today!